Les solutions pour fabriquer un acier plus vert
- A l’échelle mondiale, la sidérurgie est le secteur le plus émetteur de GES avec 7 % des émissions globales.
- En réponse à la nouvelle loi industrie verte ainsi qu’à la demande en acier et en fer, il est nécessaire de décarboner la fabrication de ces métaux.
- Selon l’AIE, l’économie circulaire est un levier de décarbonation à court terme, mais il faut surtout favoriser la sobriété.
- Des technologies « d’évitement direct du carbone » et « d’utilisation intelligente du carbone » font déjà leurs preuves, mais doivent encore être développées.
- L’UE et la France sont engagées dans une politique de relocalisation de l’activité industrielle qui pourra minimiser le coût et l’impact environnemental.
Le 11 octobre dernier, la loi industrie verte est adoptée. Elle vise notamment à décarboner les industries existantes. Un enjeu de taille : en France, l’industrie représente 18,1 % des émissions de gaz à effet de serre (GES) en 20221. La sidérurgie – l’industrie du fer et de l’acier – est l’un des secteurs les plus importants à décarboner. En France, il est le 4ème secteur industriel le plus émetteur de GES (20 % des GES de l’industrie, soit 4 % des émissions totales du pays). Mais à l’échelle mondiale, le secteur se hisse en première place : environ 2,8 milliards de tonnes de CO2 sont émises chaque année pour la production d’acier, soit 7 % des émissions globales de GES2. Or, la demande explose. L’acier et le fer sont indispensables à la construction, la mobilité ou encore la production d’énergie renouvelable – une éolienne est composée de plus de deux tiers d’acier ! À l’échelle mondiale, les besoins pourraient augmenter de plus d’un tiers d’ici 2050 d’après les projections de l’Agence internationale de l’énergie (AIE)3.
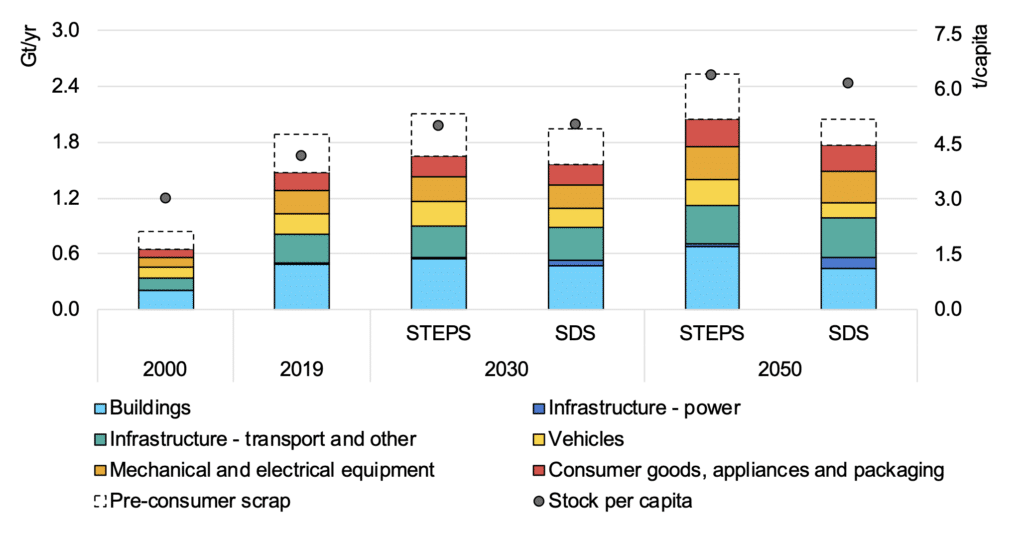
Source: IEA analysis informed in part by Pauliuk, Wang and Muller (2013), Cullen, Allwood and Bambach (2012) and Gibon et al. (2017)
Comment l’acier est-il fabriqué ?
Deux méthodes sont principalement employées à travers le monde pour fabriquer de l’acier, un alliage de fer et de carbone. 70 % sort de la filière fonte4 : introduit dans un haut fourneau en présence de coke (issu de la pyrolyse de houille), le minerai de fer est transformé en fonte par réduction chimique. Lors de cette étape, le carbone s’associe à l’oxygène contenu dans le minerai et forme du CO2. La fonte est ensuite transformée en acier dans un convertisseur. Autre procédé utilisé : la filière électrique. Cette méthode est largement employée pour recycler de la ferraille, cette dernière étant fondue dans un four à arc électrique. Quelques méthodes alternatives existent : il est par exemple possible d’utiliser du minerai dans la filière électrique. Dans ce cas, le fer est extrait du minerai par réduction directe à l’aide de charbon ou de gaz naturel, avant d’être transformé en acier dans le four à arc électrique.
Fabriquer de l’acier nécessite d’importantes quantités d’énergie : la fonte atteint par exemple 1 500 °C au sein du haut fourneau. Or, en 2019, les trois quarts de l’énergie consommée par le secteur étaient fournis par le charbon. À ce jour, le recyclage au sein de la filière électrique est la voie la plus décarbonée. Elle ne requiert qu’un huitième de l’énergie de l’acier produit à partir de minerai, et principalement sous forme d’électricité plutôt que de charbon. « Il faut augmenter la fraction recyclée, mais cette filière est limitée par la ressource : une grande partie de l’acier est, par exemple, immobilisée pour des décennies dans les bâtiments », explique Fabrice Patisson.
Plusieurs solutions efficaces à court et long terme
À court terme, l’économie circulaire est le levier le plus prometteur. Les innovations technologiques de décarbonation reposent sur un renouvellement du parc de production, dont la moyenne d’âge mondiale s’élève à 13 ans, soit moins d’un tiers de la durée de vie classique. Dans son scénario prospectif visant une réduction de 50 % des émissions du secteur en 2050, l’AIE souligne que 40 % des réductions cumulées d’émissions de GES entre 2020 et 2050 reposent sur l’économie circulaire. En clair, c’est le levier de la sobriété : en réduisant la demande, les émissions sont diminuées. Cela passe principalement par un allongement de la durée de vie des bâtiments, mais aussi par l’amélioration des rendements de fabrication, la réduction de l’utilisation des voitures et leur allègement, l’amélioration de la conception des bâtiments ou encore la réutilisation de l’acier.
En parallèle, un panel d’options d’atténuation existe. Impossible de répondre aux besoins en hausse sans produire d’acier primaire. Quel est l’un des leviers majeurs pour décarboner sa production ? Se passer de charbon. Les importantes émissions de GES de la sidérurgie s’expliquent en majeure partie par la formation de CO2 au sein des hauts fourneaux par réaction chimique, et les hautes températures requises. Le fer « vert » serait produit grâce à la réduction directe du minerai de fer par électricité ou hydrogène vert (H2), au lieu du coke. Il peut ensuite être intégré dans la filière électrique habituelle et être transformé en acier dans un four à arc électrique. Cette voie technologique est dite « d’évitement direct du carbone ». « À ce jour, le procédé de réduction directe est connu et répandu – cela représente environ 7 % de l’acier mondial – mais il repose sur l’utilisation de syngaz (un gaz de synthèse issu de gaz naturel) qui contient environ 60 % de H2, détaille Fabrice Patisson. Le plus gros challenge est de passer à 100 % de H2 à l’échelle industrielle. »
La voie hydrogène est la plus avancée : parmi les 60 projets de décarbonation de l’acier recensés en Europe en novembre 2022, 42 reposent sur l’utilisation d’hydrogène5. En Suède, le projet pilote Hybrit produit depuis 2021 les premières tonnes d’acier au monde grâce à ce procédé. Il pourrait permettre de réduire les émissions de CO2 de 85 %6. « Désormais, le développement de la filière repose sur la volonté et la capacité d’investissement des sidérurgistes », estime Fabrice Patisson. Quant aux besoins en électricité – si l’hydrogène est produit par électrolyse de l’eau, ils s’élèveraient à 370 TWh pour décarboner l’ensemble de la production primaire d’acier de l’UE7, soit 14 % de la production totale actuelle d’électricité8.
Une autre voie technologique – complémentaire à la voie d’évitement du carbone – existe : celle « d’utilisation intelligente du carbone ». Cela passe en premier lieu par une optimisation des procédés de production existants. Même si la filière maîtrise les hauts fourneaux, des améliorations restent possibles. Il a par exemple été montré que plus de la moitié de l’énergie achetée par les sidérurgistes était perdue au cours du procédé9. Utiliser les meilleures technologies disponibles et optimiser les procédés pourraient permettre de réduire les émissions cumulées du secteur de 21 % entre 2020 et 2050 à l’échelle mondiale, d’après le scénario prospectif de l’AIE visant à réduire de 50 % les émissions du secteur d’ici 2050. Cela passe par le déploiement de systèmes de récupération de chaleur, améliorer la qualité du coke, remplacer partiellement le charbon par du gaz naturel ou des bioénergies ou encore implémenter des outils de maintenance prédictive.
La capture et le stockage du carbone sont une option intéressante à court terme, avant que les technologies propres – comme l’hydrogène – soient déployées.
Utiliser intelligemment le carbone passe aussi par sa valorisation. Comme dans de nombreux secteurs industriels, la capture et la valorisation ou le stockage du CO2 sont considérés comme indispensables pour réussir la transition d’ici 2050. Pour l’AIE, elle pourrait permettre de capter 6 % des émissions générées de 2020 à 2050, avec un taux atteignant 25 % de capture par an en 2050. Seule une unité commerciale stockant le CO2 existe actuellement dans le monde, aux Émirats Arabes Unis. Quelques projets de valorisation sont en cours de développement. « La capture du CO2 est plus facile dans l’industrie sidérurgique que dans d’autres, complète Fabrice Patisson. La capture et le stockage sont une option intéressante à court terme, avant que les technologies propres – comme l’hydrogène – soient déployées. »
Enfin, l’UE et la France sont engagées dans une politique de relocalisation de l’activité industrielle. Exit les émissions liées au transport des produits. Le mix énergétique français, à l’empreinte carbone relativement faible, est également un avantage en termes d’émissions de GES. « En mutualisant les services, la chaîne logistique, l’énergie et les matières premières, les impacts environnementaux et les coûts sont minimisés. » Il est possible de diminuer les émissions de GES jusqu’à 75% si l’on compare au même parc sans coopération10. Le site d’ArcelorMittal de Dunkerque est un exemple en la matière : le laitier – un coproduit des hauts fourneaux – est valorisé en matériau de construction et la chaleur fatale est injectée sur le réseau municipal de chauffage de Dunkerque11. Deux nouveaux réacteurs nucléaires EPR doivent y être implantés, ainsi qu’une unité de production d’hydrogène vert, qui pourra alimenter la future unité de réduction directe du minerai par hydrogène d’ArcelorMittal12. « Intégrer le vecteur hydrogène dans les écoparcs permet de rendre la filière rentable, économiquement mais aussi pour l’environnement, conclut Marianne Boix. C’est une opportunité très intéressante dans ce contexte. »