The 2024 Paris Olympic and Paralympic Games are fast approaching. As part of the SCIENCES2024 project, we are working to improve the performance of the tibial prostheses used by certain Paralympians for the long jump. There are several categories of amputees – low or high leg amputation, both limbs or one limb – but we are focusing on unilateral amputees, i.e. those who have had one leg amputated below the knee.
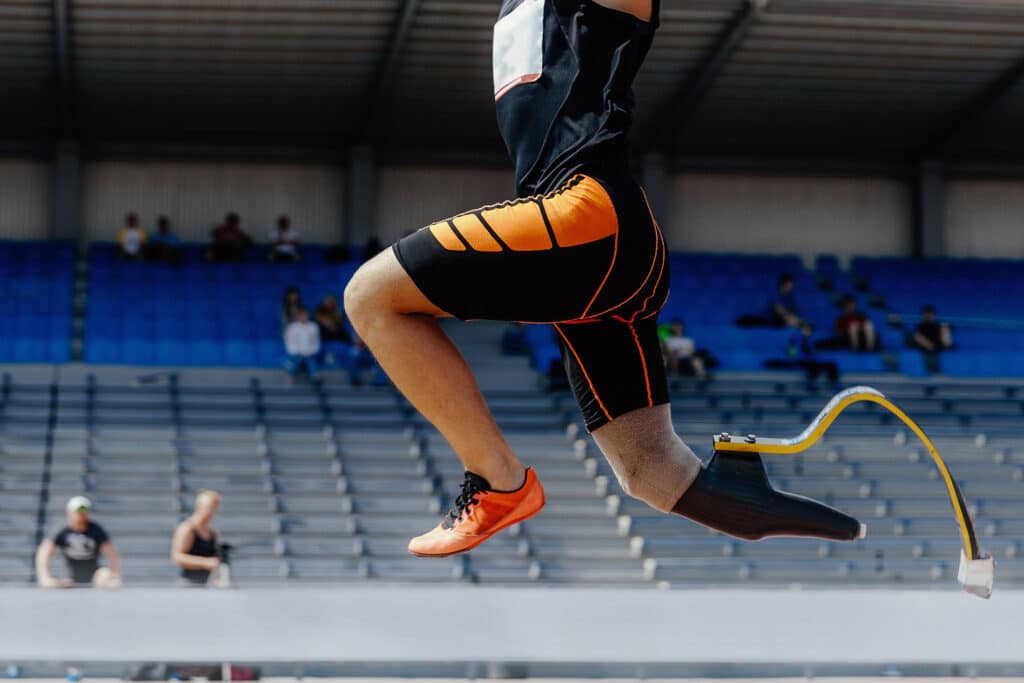
Jumping further
The aim of our approach is to find solutions to optimise the restitution of energy at the critical moment of the jump: it is the very moment of the impulse that allows the athlete to project himself forward. In unilateral amputees, the jumping blade – made of rigid but very slender carbon – replaces the amputated limb and is like a large, almost perfect spring.
The blade, which fits over the residual limb, allows the athlete to take off by pressing on it and thus compressing it strongly at the moment of impulse. During a long jump, an athlete makes a long run-up: the faster he or she runs, the more kinetic energy he or she stores, which is then “transformed” into impulse during the final take-off. The main challenge is to convert this kinetic energy, linked to the speed of the run-up, into “impulse energy” to enable the athlete to run as far as possible.
The main challenge is to convert the momentum into impulse energy to allow the athlete to run as far as possible.
Certain parameters, such as an unsuitable jump angle, a poor body position or the athlete’s own movements during the jump, can dissipate this precious energy. In addition, friction in the socket or shock to the athlete’s body can lead to injury – even if the gesture or prosthesis is designed in the best possible way for performance. We are therefore looking at how to optimally transfer this kinetic energy to the impulse in a length-efficient manner without causing injury that is detrimental to performance.
The sports gesture and the prosthesis are therefore essential for energy conversion. To this end, we study the energy accumulated in the blade so that the athlete can project as far as possible. We are more interested in performance in this part of our work, and we work with the technical director of the French Handisport Federation who puts us in contact with the athletes and their trainers.
Improving comfort
So, in addition to improving performance, we also seek to improve the comfort of the athletes, to limit their fatigue and, of course, their injuries. The jumping blade is an appendage that allows them to jump, but it also creates vibrations and shocks when it hits the ground. These vibrations can cause friction in the socket, leading to discomfort and even pain. We are looking to measure these shocks through numerical modelling to analyse their transmission to the athlete’s body.
We will be able to understand how the materials making up the blade and the prosthesis can deform mechanically and reduce the shock.
We have set up experimental protocols in the laboratory that will enable us to reproduce the sporting gesture. With these, we will be able to understand the overall deformation of the blade, under the effect of compression, during the impulse, but above all we will be able to understand how the materials making up the blade and the prosthesis transmit the forces of the track to the athlete’s body. In addition, we will identify their role both in the restitution of energy and in the reduction of the risk of injury inherent in the practice.
To do this, we have developed numerous laboratory experiments with various instruments. High-speed cameras and sensors allow us to analyse dynamic phenomena in detail and to measure efforts and wave transfer. These measurements allow us to move towards a global optimisation of the blade-prosthesis system.
We are also working on the development of the materials that make up the prosthesis and we are trying to find those that will give good overall performance. These materials are manufactured by 3D printing, otherwise known as additive manufacturing.
Understanding the forces
To best analyse the impact of materials and athletic movement, we are looking at two scenarios. In the first, when the athlete presses on the blade slowly enough, this causes a progressive deformation. In this case, the information can be analysed in a fairly simple way through a static laboratory test protocol. Since the blade is made of a rigid but slender material, it deforms globally but also locally at the sole and at the point of contact with the residual limb via the socket. We are therefore studying the local static deformations, which allow us to understand how energy is dissipated, and the nature of the pressures on the amputated limb, which can lead to possible injuries.
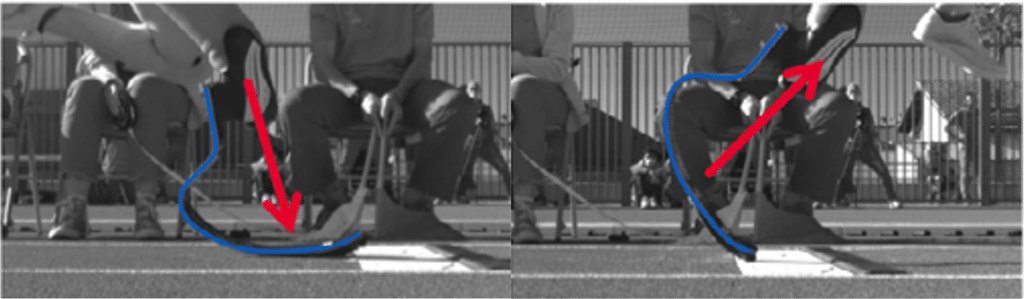
Second scenario: the speed of the load is progressively increased to reproduce the conditions of the athlete’s last impulse on the blade. Thanks to our observations during the athlete’s run and at the moment of his jump, we are able to measure the deformation speed of the blade and the sole. The transmission of vibrations and shocks from the ground to the blade and then to the athlete’s limb is thus characterised by theoretical models. In this second scenario, it is also interesting to see the dynamic effects and forces that interact between the track, the blade, and the athlete. These forces vary rapidly at the moment of impulse and are representative of the impact phenomena that often lead to injuries.
In the first scenario, static forces are at work; in the second, dynamic or impulse forces are at work. These concepts are commonly used to study structured materials or metamaterials in industry. We transpose them to the service of humans, to advance the field of “augmented human” or the future medal-winning athlete!
Isabelle Dumé
Références