3D printing: unexpected ecological benefits for industrials
- Danish companies are concerned about environmental sustainability, but do not usually think about improving the circular economy of their products.
- 3D printing, originally intended for product development tasks, actually has unexpected benefits in terms of sustainability.
- Firstly, the technology can improve companies' use of materials and reduce waste.
- With 3D printing, companies can also go from idea to product much faster and with less CO2 emissions from logistics.
- Finally, this technology can support companies' efforts to minimise their environmental impact through more circular economic paths.
Of all emerging technologies, 3D Printing (or additive manufacturing) certainly made the top list of those that were predicted to “change the world”. Yet, nearly 40 years after is conception and 10 years after the 3D printing ‘hype’, it is hard to find situations where 3D printing has had a radical impact, aside from a few specific niches such as prosthetics and the aerospace industry.
Among the predicted benefits of 3D printing was its positive impact on sustainability, by allegedly offering “waste-free manufacturing”. The promise was that only the quantity of material needed in production are actually used. As such, products can be manufactured on demand with only raw materials being transported and so on. Yet, so far, this promise has also struggled to materialise. However, there may be light at the end of the tunnel. As the study presented in this article indicates, where 3D printing has been implemented in industry, it would seem to be a driver of sustainability – particular as a circular economy enabler.
Thierry Rayna, Tech4Change Chair
Since 2018 the University of Southern Denmark has been mapping the use of 3D printing by Danish production companies, together with the Danish Additive Manufacturing Hub. Their latest report from 20221 based on interviews and survey data from autumn 2021, analyses the link between use of 3D printing technology and the companies’ approach to ecological sustainability. All production sites of firms in manufacturing industries with more than 10 employees were invited to participate.
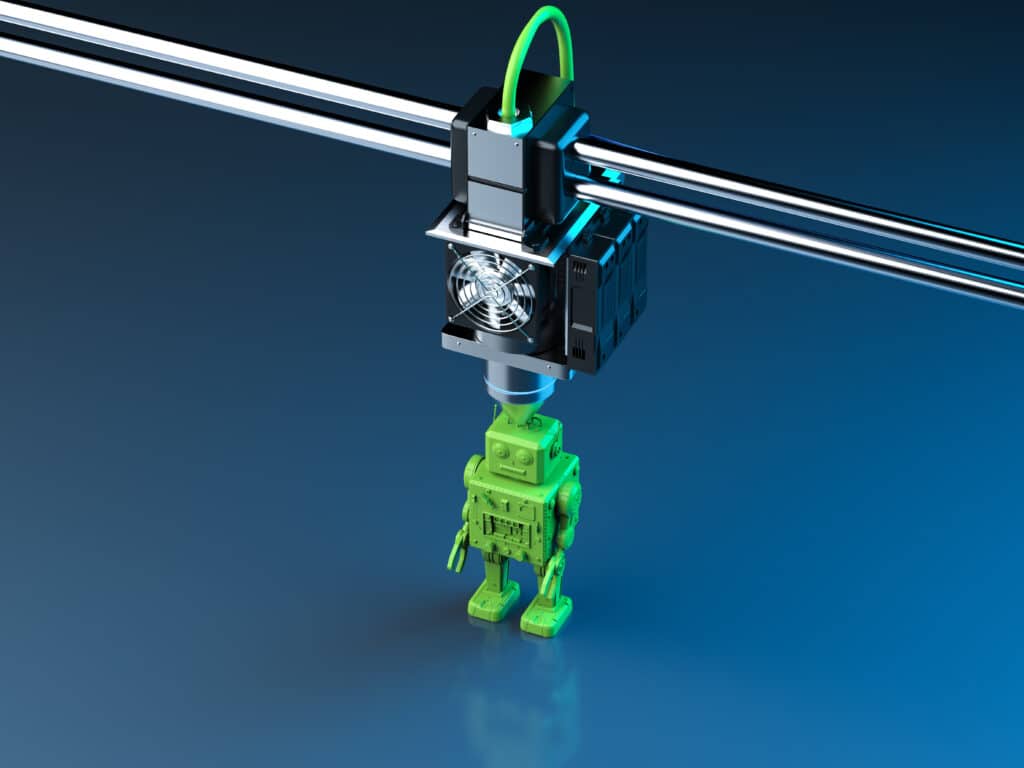
Overall, Danish companies generally reported that they have a strong focus on ecological sustainability. As there are multiple sources of sustainability and ways to improve, a more detailed investigation highlights some interesting trends. First, sustainability has commonly been associated with reduction of water and energy use in industrial firms but there is also now a new, strong focus on reducing material waste during production – with just over half the companies focusing on optimising the way they use their products.
However, much less attention is paid to improving circular economy of products. As such, almost half the companies reported no or very little focus on prolonging the lifespan of their products through offering spare parts, repair services or “take-back” at end-of-life of products. Moreover, many of the companies have no or very little focus on optimising product lifespan and recycling in general.
3D printers in industry
3D printing is an additive technology, using a 3D drawing (STL-file) as a template. Most processes use liquid material, powder or solids that are applied layer upon layer to produce an object. Depending on the equipment used, the object can be made from plastic, metal, ceramics, composite, or even concrete (currently in development by companies such as Create SDU2). Companies typically use 3D print technologies in product development, to print objects that support production like tools, or to produce parts of final products or spare parts. Companies’ access to and engagement in 3D print technology is in part determined by their ownership of the technology – companies either own or lease printing equipment to have the equipment in-house, or they may outsource them.
Unexpected benefits
In 2018 and 2019, a quarter of Danish manufacturing companies reported using 3D print technology, while the share had increased to a third in 2021. The primary use of 3D printing is for product development tasks. It both facilitates design of new products and speeds up the process as the site can print and test prototypes as needed. Of those, 80% report that they either own or lease the equipment – meaning they have it physically present within the company. The remaining 20% companies buy 3D printing services from subcontractors. For example, Boeing now has a division for 3D printing industrial parts for both submarines, helicopters, and planes.
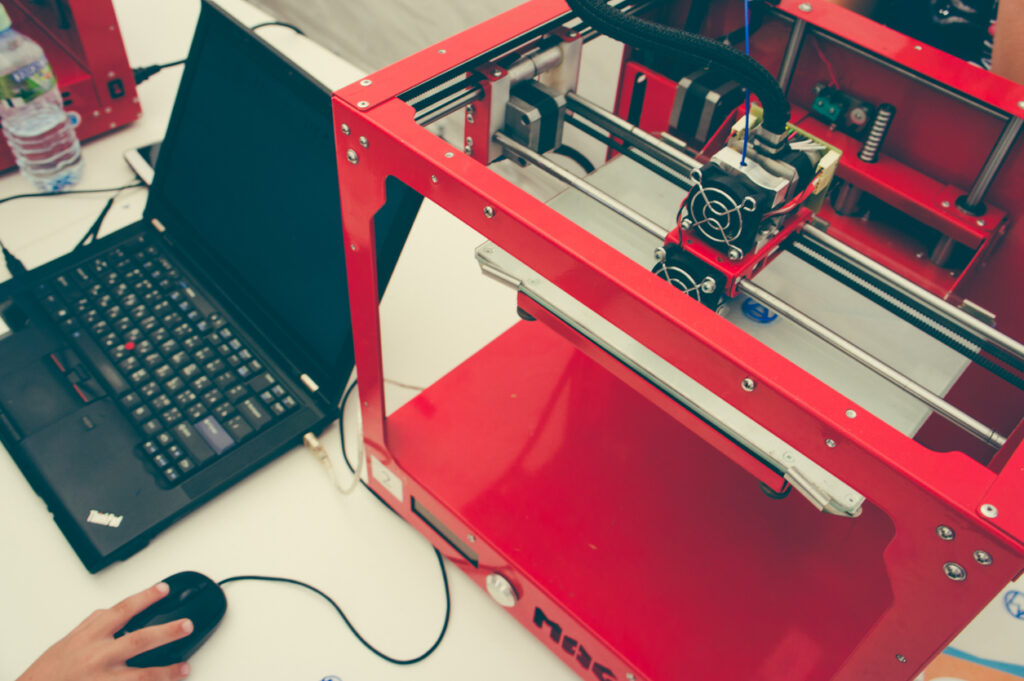
Companies describe the transition from a slow-moving process of sending specifications to sub-contractors abroad and waiting several weeks to receive back prototypes that often had to be repeated several times, to overnight printing. 3D print technology enables companies to get from idea to product much faster with less CO2 emissions from logistics and less waste.
Of those, a local company, Jydsk Emblem Fabrik, produces medals and emblems for a range of private and public customers including the Danish army. The firm has worked strategically over the last 10 years to move its production back to Denmark to reduce costs and time usage of logistics, whilst allowing the company to ensure a high-quality, flexibility and maintaining a short time from design to production. 3D print technology has enabled this process and simultaneously facilitate more environmentally friendly production and reduced CO2 emissions from logistics in both development and production.
Other examples include Jørgensen Engineering, a robotics integrator, that increasingly applies 3D printing. The firm first used 3D print in 2016, they now own FDM technology and use it to test and print prototypes, while they use subcontractors for 3D printing of production equipment.
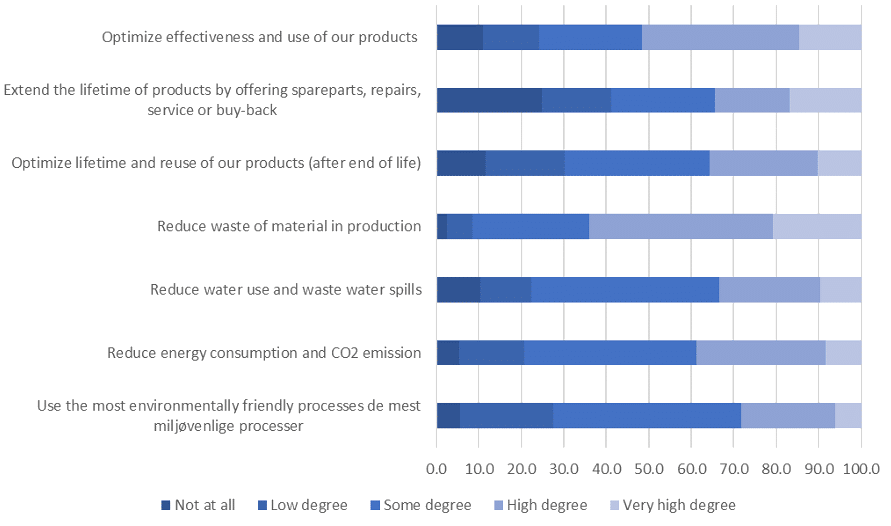
The companies that use 3D print technologies report that they engage with initiatives to increase the sustainability of their business more often than the companies that do not use 3D printing. In particular, they are more often focused on aspect pertaining to the circular economy. This is surprising, given that most of the companies declare that they did not originally adopt 3D print technology with the intent of increasing the sustainability of their business. And, although there is a wide agreement that 3D printing is not a “sustainable technology”, the companies report unexpected sustainability effects in relation to their implementation of the technology.
Improved sustainability
There are multiple reasons for this. First, 3D printing can improve companies’ material use and reduce waste. Waste reduction can be achieved directly through use of less material as 3D print is a layer-by-layer additive technology which enables completely new designs using less material. Second, 3D printing can reduce CO2 emissions related to logistics, as companies avoid the time-consuming process related to manufacturing prototypes and tools for production in low-cost geographies, or transport of spare part to remote locations. Third, 3D printing can support companies’ endeavour to minimise their negative impact on the environment through more circular economic paths where product life is expanded through services, spare parts, extensions and upgrades, and products are designed for disassembly and recycling at end-of-life. In a not-too-distant future many companies hope to be able to reuse materials from end-of-life products to create new components or even entire products.
When we compare the motivations for why companies adopted 3D printing (i.e. what they expected to gain) with the effects the companies experience 3D print to have on their business, the companies experience more sustainability effects than they expected prior to adopting 3D print technology. Having identified the possible sources, in the report we compared the original motives with the achieved effects to identify the potential benefits to be captured. What we noticed is that there may be greater effects with respect to sustainability to be achieved than expected. 10–15% of the companies have positive effects on sustainability with respect to development of product that are easier to recycle, reduction of number of components in the final product, and reduction of material consumption and waste. This can be seen as an opening for future increased use of the technology.
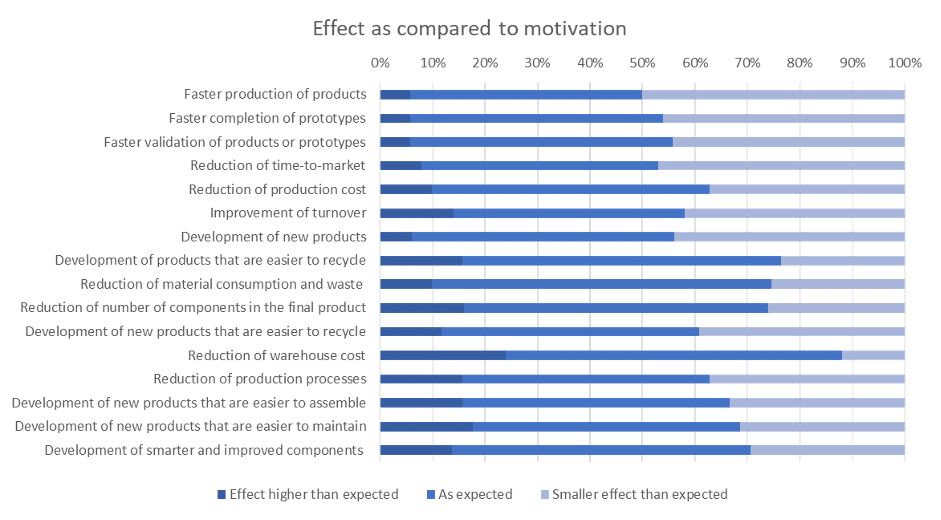
The main findings of the study are that a growing share of companies that implement 3D printing not only facilitate and accelerate innovation, but also manage to develop more environmentally sustainable products and forms of production. Although 3D printing is not in itself a sustainable technology, it can promote sustainable business processes. Improved sustainability can be both the result of a conscious strategy and a side effect of the implementation of new technologies such as 3D printing. It is important for companies to be aware of how 3D printing can contribute to their environmental sustainability, whether they are implementing 3D printing to reduce costs, accelerate innovation or to improve the sustainability of their business.