Reducing the carbon footprint of the construction sector relies on a number of different factors. Circular economy, eco-design, energy renovation… and new materials. The manufacture of materials for building construction accounted for 10% of global CO2 emissions in 2020, equivalent to 3.2 Gt of CO21. And demand is growing: global cement consumption rose from 900,000 to almost 2 million tonnes between 2000 and 2015 (it dropped slightly in 2020 due to the public health crisis). Cement and steel are the main contributors, followed by aluminium, glass and insulating materials. Biobased materials are a good alternative for the sector.
Conventional or bio-based?
The structure, insulation and cladding of a building can be made from biobased materials. Derived from biomass of animal or (more often) plant origin, biobased materials on the construction market are varied: timber, cellulose wadding, shives or flax shives, wheat straw, etc. However, they are currently used very little: only 12% of the materials used in construction are biobased2. Moreover, these materials are sorely lacking in a sound regulatory framework for the environment: the European standard (NF-EN 16575) considers as a biosourced material any product derived entirely or partially from bioresources…
Each kilogram of wheat straw contributes to storing about 1.4 kg of CO2.
A private label goes further by distinguishing materials incorporating a minimum threshold of biobased material, set at 70% for insulation or 25% for plant-based concrete3. In France, the state label “Bâtiment biosourcé” (biosourced building, in English) concerns new buildings. To obtain it, a single-family house must incorporate between 42 and 84 kilograms of biobased material per m2 of floor area, depending on the grade required. These figures fall to 18 to 36 kg/m2 for a collective dwelling.
“The manufacture of conventional materials contributes to the removal of carbon stored for millions of years in the soil and its injection into the atmosphere,” explains Thibaut Lecompte. “The sector’s priority must be to reuse materials, and then to use bio-based materials”. The main advantages of biobased materials? Unlike conventional materials, they store carbon. “Plants capture the CO2 contained in the lower atmosphere during their growth,” he explains. It then remains stored within them for the entire life of the building, and even longer if the material is reused!” For example, each kilogram of wheat straw contributes to storing about 1.4 kg of CO24. The captured carbon is eventually released into the atmosphere at the end of the material’s life, for example if the wood is burnt for heating. Biobased materials therefore have a double advantage: they sequester atmospheric CO2 for decades, but also avoid depleting soil carbon by replacing conventional materials.
A range of possibilities
The opportunities offered by the different alternatives vary. Let’s look at wood, the most commonly used bio-based structural material. “Timber framing limits thermal bridges and allows large openings to be made while facilitating implementation, unlike steel or concrete,” points out Thibaut Lecompte. Forests are the second largest carbon sink in the world, helping to store 10 billion tonnes of CO2 equivalent5. However, virtuous forestry must be managed sustainably, by limiting clear-cutting, monocultures and the use of phytosanitary products 6.
In Europe, we remove less wood than is produced each year (73%): this equilibrium needs to be preserved if the carbon balance is to be maintained.
“The biomass extracted must also be compensated through production,” adds Thibaut Lecompte. “In Europe, we remove less wood than is produced each year (73%): this equilibrium needs to be preserved if the carbon balance is to be maintained for example by reducing our consumption of firewood in favour of timber.” A European research team estimates that the area of forestry needed to supply timber or insulation can fully meet the demand: it represents only 23% of the land already used for construction, and would therefore not generate any land pressure or intersectoral competition7.
Another approach is biosourced walls, incorporating biosourced insulation and plant-based concrete. “Biosourced materials are particularly effective when it comes to improving thermal comfort,” says Vincent Picandet. Thanks to their ability to absorb and release water in the form of vapour, humidity inside the building is better regulated. Even though conventional insulation materials often have lower thermal conductivity, they are much less effective, if not totally ineffective, at regulating humidity,” he continues. Unfortunately, the greater comfort offered by bio-based materials is not reflected in current standards, which only measure thermal conductivity. To date, only 11% of roofing renovations are carried out with biobased insulation (this figure falls to 7% and 4% respectively for walls and floors)8.
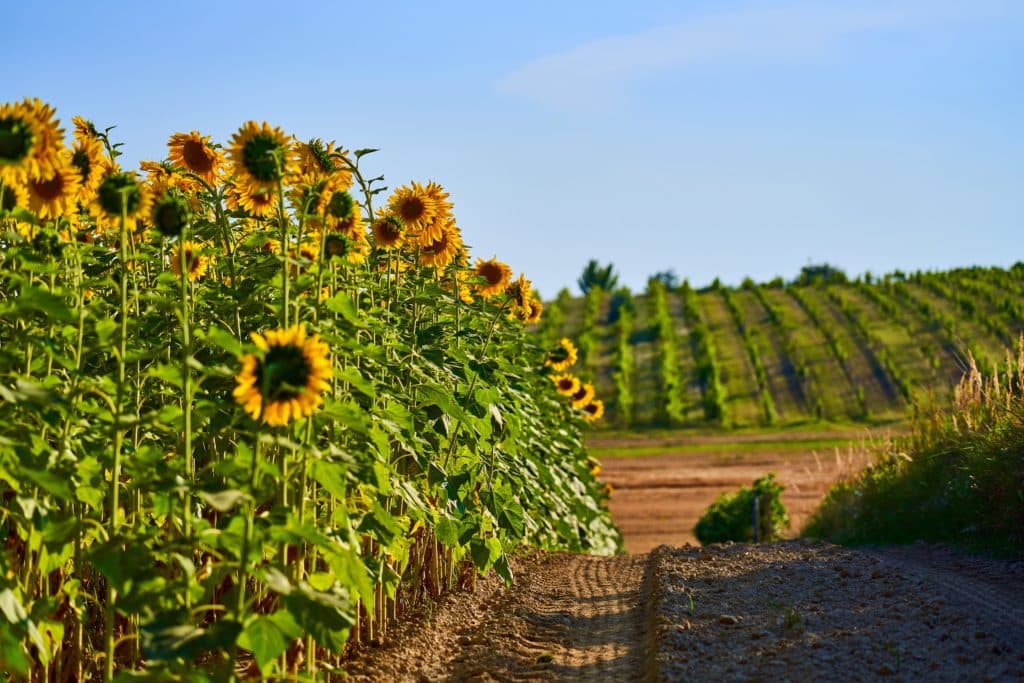
However, they do have one drawback when compared to conventional materials. “Proper installation must be observed to ensure that the entire wall breathes properly,” says Vincent Picandet. This makes their use more complicated in renovation. “But if the right installation conditions are respected, these materials have the same durability as conventional materials over a period of half a century,” Vincent Picandet explains. We don’t have the necessary hindsight for much longer than that. For the researcher, the “Hemp concrete is less durable than traditional concrete: but the standards require us to build buildings that are more resistant than necessary!” Of course, conventional concrete will always be needed for civil engineering works or structural functions. But concrete made from plant aggregates can be used as a substitute for conventional insulating materials or for the composite walls that are commonly used.
Carbon footprint
From a climate point of view, the life cycle analysis (LCA) of the annual plants used for insulation or biosourced concrete (hemp, wheat, flax, sunflower, etc.) is very positive. In a few months of cultivation, they sequester carbon, which is then stored in the material throughout the life of the building. The carbon impact of the implementation of an entirely biosourced wall (composed of a wood frame and straw insulation, with a lifespan of 50 years) is evaluated at nearly 4 kg CO2e, compared to 49 kg for a conventional solution9.
The construction sector would only need 12% of the land already available for construction if wheat straw were used as insulation.
The potential is there: the construction sector would only need 12% of the land already available for construction if wheat straw were used as insulation, as a large part of it is not currently used. This is not the case for hemp and cork, which are not widely cultivated today. “To maintain an attractive carbon footprint, it is necessary to maintain a balance in land use: do not replace a forest with a field, for example,” warns Thibaut Lecompte. For example, hemp and flax can be introduced as an intermediate crop. In an article in The Conversation10, researcher Hélène Lenormand gives an overview of all the plants available for insulation: “If there is competition between different applications, the annual supply is so huge (15 million tonnes in France) that all the different uses can be supplied without fear of any competition. The different sources are complementary both geographically and temporally, ensuring the availability of the resource. This is a major advantage compared to other conventional imported materials.
Despite this, the bio-based materials sector is still underdeveloped. Few figures exist. Biobased insulation has grown by almost 40% in 3 years, to reach 10% of the market according to industry professionals11. The arrival of the new French thermal regulations could change things: the RE2020 – applicable to new buildings – integrates the carbon impact of the materials used through their LCA, as do Denmark and the Netherlands. And around the world, more and more countries are introducing regulations – including the carbon footprint of materials – aimed at achieving zero carbon by 205012.