The wind power industry is facing a major turning point. The fleet is aging. In Denmark, 50% of wind turbines are over 15 years old, and 40% in Germany1. Although wind turbines are designed to last about 20 years, the age of renewal in Europe varies from 9 to 27 years. In France, only a small part (less than 5%) of the installed capacity is older than 15 years, and Ademe points out that most renewals could take place between 15 and 20 years. In the coming years, the potential for renewal will even accelerate in Europe: it could increase from 3 GW per year in 2020 to more than 6 GW in 2030 according to Windeurope2.
Managing waste from wind turbines
So a new question arises: how do we manage the waste from dismantled wind farms? According to DREAL Grand Est3, 90% of wind turbines are made of concrete (840 tons on average) and steel (246 tons). These materials are easily recycled and have significant markets. Other materials such as cast iron and copper are also recycled. The second-hand market is also well developed and includes major European players. « More than 90% of the mass of a wind turbine can already be recycled in France, these markets are well structured and will be able to absorb larger volumes, » says Amandine Volard, a renewable energy engineer at Ademe.
More than 90 percent of the material from a wind turbine can already be recycled in France.
Only the blades pose a problem today. They are made of a composite material: a mixture of polymer matrix (epoxy resin, polyurethane, or polyester) and reinforcing fibres (mostly glass or carbon for offshore wind turbines). The ideal? Recovering each of the materials to reuse them. However, « it is very complicated to separate the matrix and the reinforcing fibres, » explains Céline Largeau, head of the Zebra project at IRT Jules Verne. There are several separation methods: pyrolysis (thermal), solvolysis (chemical), gasification and grinding.
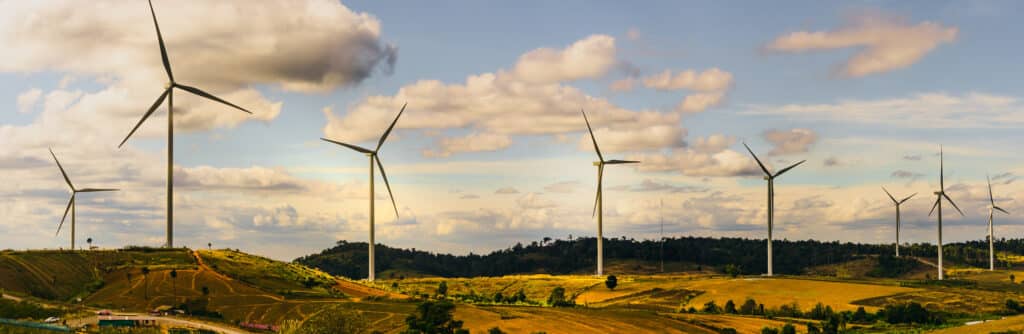
These processes allow the recovery of the fibres and/or the matrix, however, no efficient recycling process is in place today4. Some processes are fully developed and used on an industrial scale, such as pyrolysis and grinding, but they strongly degrade the physical properties of the glass fibres. The recovered fibres are more expensive and of lower quality than non-recycled fibres, and the process is not economically viable. Solvolysis, on the other hand, allows the recovery of undamaged glass fibres and a reusable resin.
10,000 to 15,000 tons of composites from the wind energy sector will need to be processed each year from 2028 in France.
But the process is not efficient, requires large quantities of resources – solvent, water, energy – and has not yet been sufficiently developed. As a result, to date, only the incineration of blades in cement plants has been developed, for example in Germany, where the renewal of wind farms is already significant5. The composite is used as fuel and the residues are incorporated into clincker, a constituent of cement. We estimate that 10,000 to 15,000 tons of composites from the wind power sector will need to be processed each year in France from 2028 onwards6, » explains Amandine Volard. But the cement industry is already in demand in sectors other than wind power and will not be able to process such quantities on its own.
Recovery, recycling and reuse
Driven by a number of factors (see box), the industry is developing new ways of recovering old blades. Some separation processes that are not yet fully developed – solvolysis, gasification and high-voltage fragmentation – are being tested. Mature processes such as pyrolysis are being improved in order to obtain output fibres with interesting properties. The R3FIBRE project7, led by Bcircular, for example, makes it possible to integrate recycled fibres into commercial cement to improve its performance. Other initiatives focus on the value chain. “One of the objectives of the Zebra project is to identify new sectors that could use fibres from wind turbines,” explains Céline Largeau. “The automotive industry, for example, is a prime sector.” Reuse is another possibility. In its analysis8, Bax & Company points out: « For the moment, recycling is getting the most attention, even if it is not the most desirable waste management strategy. » Indeed, the authors point to the possibility of directly reusing the blades for example for building facades.
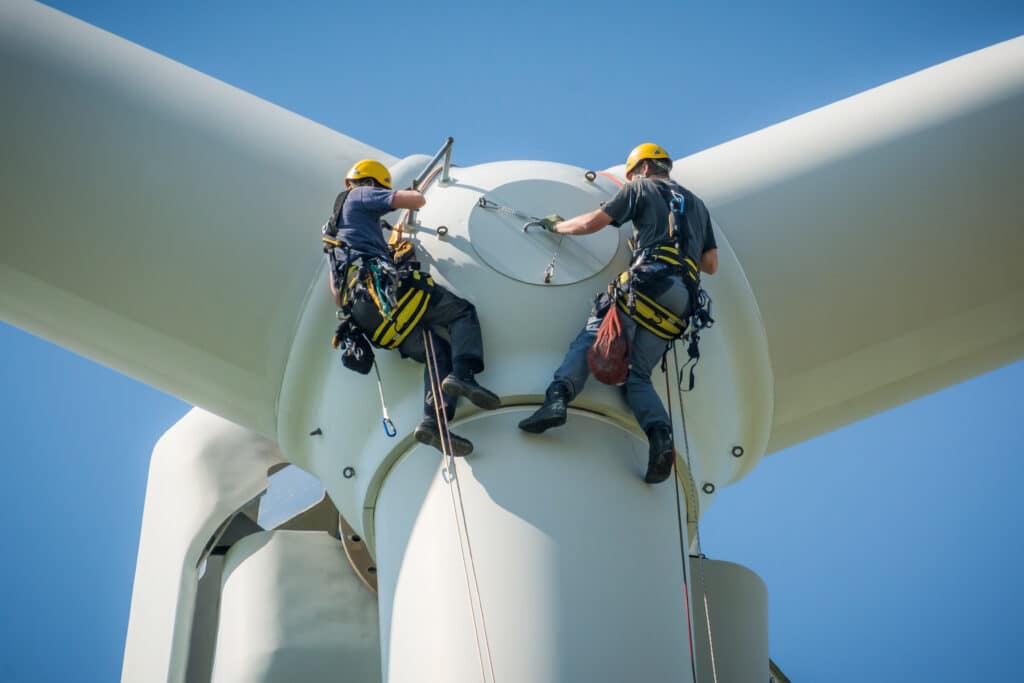
Another key area of action is the development of innovative, fully recyclable blades. Zero waste has been invited to the table by manufacturers who are aiming for this goal by 20409. Siemens Gamesa has already been marketing the first fully recyclable wind turbine blade, the RecyclableBlade, since 2021. Composed of a new resin and glass fibre, the composite material can be separated at the end of its life by chemical means. In France, the ZEBRA project led by the IRT Jules Verne is focusing on another innovative resin for the sector, thermoplastic resin. Combined with a high-performance glass fibre, the resulting composite material can be chemically recycled. « The glass fibre developed by Owens Corning can incorporate a certain amount of recycled glass fibre, which means that this resource can be reused, » says Céline Largeau. The resin can also be reused. One of the challenges of these new blades is to characterize their carbon footprint over their entire life cycle (LCA), because this has never been done before, » says Largeau. We will soon be able to provide the LCA of the Zebra blade, and the results look promising. »
THE INDUSTRY IS BEING PUSHED TOWARDS RECYCLING
The industry is preparing to deal with growing wind waste streams in a strained context. The June 22 decree10 on wind power installations requires that 90% of the total mass of dismantled wind turbines be reused or recycled by July 2022, and 95% by January 1, 2024. « However, Amandine Volard points out that these targets have already been reached by the first wind farms dismantled in France. Economic incentives – such as the inclusion of the recycling rate in the scoring criteria for the latest offshore wind tender – are also an important catalyst for the industry to evolve. » Another recent change is the economic crisis. « The manufacture of glass fibre requires a lot of energy, so costs have risen sharply in recent months, » says Céline Largeau. « This makes recycled fibre more competitive on the market. » She continues: « Finally, public opinion plays a very important role: incineration or landfilling of waste does not reflect very well on the industry.