In 2021, 53.8 million tyres – across all categories – were placed on the market1. That’s more than 567,000 tonnes of a mixture of rubber, carbon, silica, steel, textiles, and chemicals. And yet tyres have a lifespan of just a few years… Do you know what happens to our used tyres? In the same year, over 532,000 tonnes of tyres were collected, giving a national collection rate of 111.5%2!
Since 2003, organisations that place tyres on the French market – manufacturers, distributors, etc. – have been obliged to take responsibility for tyres at the end of their life cycle, based on the principle of extended producer responsibility (EPR). In Europe, despite there being no specific legislation governing the sector, two directives apply. As a result, many European countries are implementing EPR or other schemes to ensure the collection of used tyres. In a study of 51 countries around the world3, it is estimated that more than 17 million tonnes of end-of-life tyres are collected each year, leaving 8 million tonnes uncollected. China, the United States, Europe, Canada, India and South Korea are among the biggest and/or best collectors.
We need to recover used tyres in one way or another
Once they have been collected, they can be recycled in a variety of ways. In France in 2021, 15% of used tyres will be reused. Most of the used tyres collected (46.8%) are recovered for energy purposes, almost exclusively in cement works. In this case, instead of using fossil fuels, tyres are used as an alternative fuel to produce the energy needed for cement kilns. The final way of recovering used tyres is through recycling. By 2021, 35.8% of used tyres will be recycled. Reduced to aggregate, melted down in cement works or steelworks, or shredded: a whole range of new lives open up for tyres recovered as materials. “Most of the tyres we recycle are transformed into moulded objects – such as speed bumps – sport pitches, drainage material or are used in steelworks to replace some of the anthracite”, explains Jean-Philippe Faure from Aliapur. In 2010, the organisation assessed the environmental impact of substituting end-of-life tyres for products from different sectors4. The benefits are clear for Astroturf, moulded objects and cement works, but minimal for retention basins. A number of environmental indicators exist. For example, substitution for Astroturf avoids the emission of 3 tonnes of CO2 equivalent for each tonne of used tyres recovered. The process also uses 15 m3 less water.
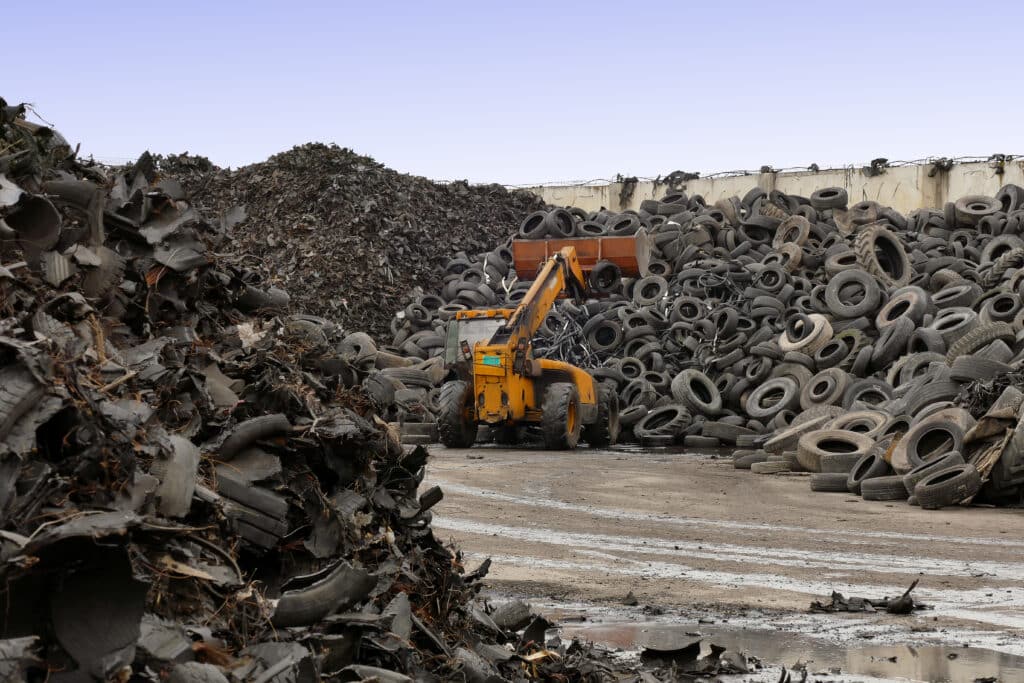
Material recovery from used tyres is the preferred method of recovery under the Environment Code5, after re-use. However, most end-of-life tyres are recovered in the form of energy. “This situation is specific to France; we don’t see the same trends in other European countries,” explains Jean-Philippe Faure. “But it’s a one-off situation and linked to recent European regulations – aimed at banning the incorporation of microplastics and the use of rubber granulates in synthetic sports pitches.” Another obstacle to recycling is the possible outlets. “We need to recover used tyres in one way or another, and the energy recovery requirements of cement works mean that they can absorb large volumes. We need to create ways of recovering materials that require large volumes, and therefore with sufficient added value.” says Ludovic Moulin. Tougher regulations could, however, push the industry to increase the proportion of end-of-life tyres recycled. “In 2020, the anti-waste law imposed a new tightening-up on the sector: companies must be accredited,” explains Thomas Grandin. This requirement will be laid down in a decree and an order6 in 2023, setting out the specifications for the sector’s eco-organisations. These impose recycling targets on the tyres collected: from 40% in 2024 to 42% in 2028 of the quantities of waste collected. “We have also noted that social acceptance is a barrier, but there is no technical barrier to recycling,” asserts Jean-Philippe Faure.
Aiming for zero waste thanks to pyrolysis
Tyres are made up of over 200 different materials. But fully developed separation processes do exist. The aim is to isolate the different components to offer products with a high added value. “For some years now, the trend has been towards the development of pyrolysis,” points out Ludovic Moulin. By heating the tyre to a very high temperature and in the absence of oxygen, it is possible to recover a number of products: carbon black, pyrolysis oil, steel-metal reinforcements, gas, textiles, etc. Although still marginal in many countries, this process is the main way of recovering end-of-life tyres in China, Thailand, Indonesia and Mexico, “because of insufficient or non-existent environmental constraints,” explains Ludovic Moulin. “Between the health crisis and fears about raw material supplies, the circular economy is gaining momentum and the market is now opening up to these new products,” comments Thomas Grandin. In Europe, Michelin has announced the creation of the first pyrolysis site with Swedish start-up Enviro, which is set to handle 1 million tonnes of used tyres by 2030. “Other projects are underway in Germany (Pyrum Innovations), Spain (L4T and Greenval Technologies) and the UK (Bolder Industries),” adds Jean-Philippe Faure. “This approach is set to take off in the next few years.”
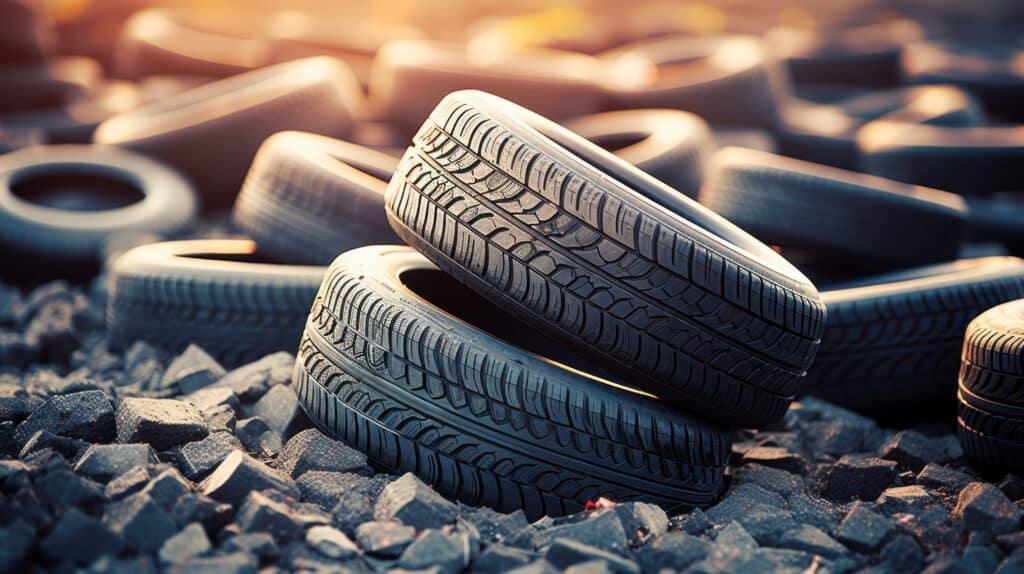
Funded by the European Union and coordinated by Michelin, the Black Cycle project7 aims to demonstrate the viability of the circular economy for pyrolysis. The consortium aims to optimise the pyrolysis process. The aim? Zero waste. Both the carbon black and the pyrolysis oil – transformed into carbon black – recovered will be entirely reused to manufacture new tyres. Other projects aim to explore new ways of recovering used tyres. “Public works are the most promising sector for the future,” says Jean-Philippe Faure. “For example, there is a need for new types of backfill, capable of absorbing shock and being light and flexible.” Recycled tyres could even be incorporated into pavements using a mixture of recycled concrete and rubber aggregates8.
In France, the joint laboratory for advanced materials recycled by vapothermolysis (Marvapol) is also working on the creation of new products to make the most of used tyres. “Vapothermolysis is a thermochemical separation process, on the borderline between pyrolysis and solvolysis [editor’s note: a dissolution process using a solvent],” explains Ludovic Moulin. “We use superheated steam at ambient pressure to separate the reinforcing fillers from the rubber.” What is the advantage of vapothermolysis? This separation process produces recycled carbon black with different properties that are of interest to manufacturers. “The output oil is also recovered as a material, a product that is now of interest to the chemical industry,” comments Ludovic Moulin. A plethora of possibilities are opening up for tyre recycling in the future.