In the photovoltaic industrial chain – from quartz to electron – it is often said that silicon is abundantly available on our planet. But, contrary to the commonly used expression, this abundance in the Earth’s crust has nothing to do with its industrial availability. To extract so-called ‘metallurgical’ silicon (99.8% pure), very special quality quartz, low-ash reactive coal, wood and electrical energy are required. Of the 3.5 million tonnes manufactured worldwide, China produces around 75%, while Europe produces only as much as 17% of its own consumption.
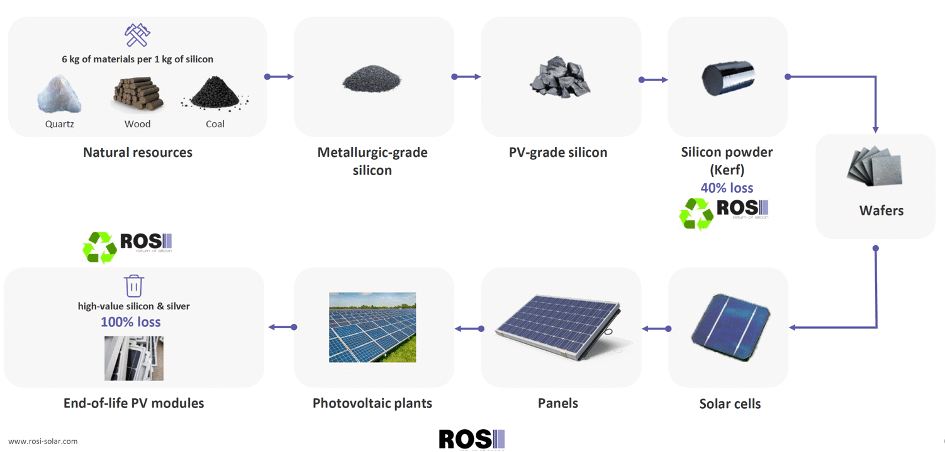
This silicon must be purified to a purity of 9N (99.9999999) in order to be processed into photovoltaic “grade”. However, Europe and the United States, which were leaders in the 2010s, have become marginal in the production of this material. Only the German company, Wacker, has managed to remain a major player, thanks to its quality, even if the pressure exerted on prices and anti-dumping measures have been enabling Chinese producers to obtain a current market share of more than 90%. The following two tables illustrate this*:
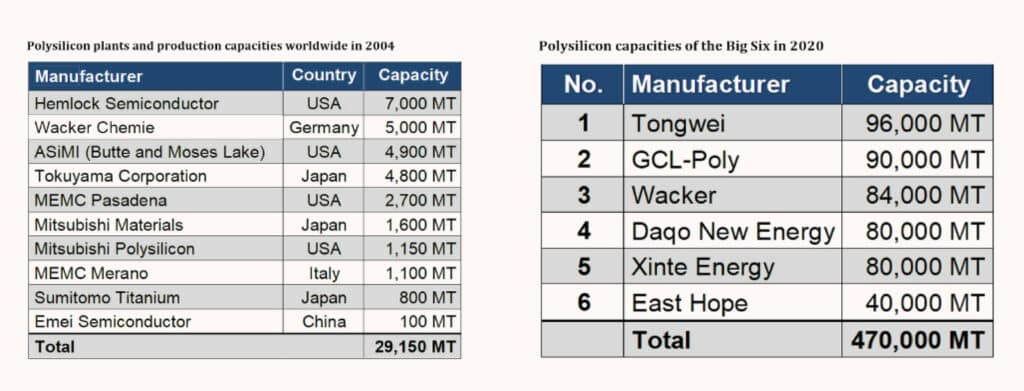
In 2022, 827,000* tonnes of PV silicon were manufactured in China compared to about 40,000 tonnes in Germany. Given the processing yields, it takes about 6 tonnes of scarce natural resources to produce one tonne of photovoltaic silicon or “polysilicon” (5.8 T/T to produce Mg-Si, and then a minimum of 5% loss in the conversion of Mg-Si to PV-Si).
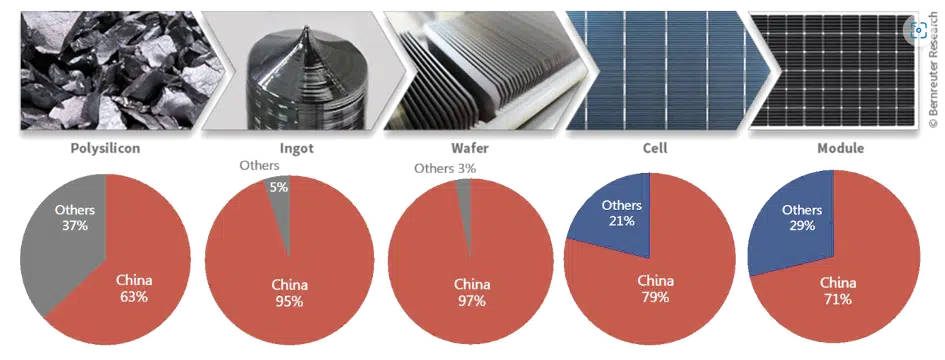
From polysilicon to electron
The next step is to transform this pure material into ingots, which are in fact more than 83% monocrystalline. The search for high photo-electric yields is turning players away from polycrystalline ingots, while the ‘semi-mono’, a French curiosity, is non-existent. At this stage, about 35 to 40% of the silicon is lost, transformed into kerf – a nanometric suspension of chips that is very difficult to use. Wafers are then obtained. Here again, China has captured most of the world’s production with 357 GW equivalent. Only one European producer is still operating (NORSUN in Norway).
The wafers are then transformed into cells, a process that requires 7–12 steps depending on whether PERC, TOPCON or HETEROJONCTION technologies are used. It is at this stage that the silver collectors are put in place. In 2020, PV was already consuming 3000 T/year or 10% of the world’s available silver. This has increased to 13% by 2022. China produced 318 GW equivalent in 2022 and forecasts to 2030 make silver extraction untenable without recycling.

Finally, the assembly of cells, interconnected by copper-based collectors, is encapsulated between two sheets of EVA to withstand about 20 years of weathering, and then glued under a sheet of glass, with an aluminium frame, to become a module. There is a strong trend towards increasing the number of cell formats, both whole and half cells, to optimise the efficiency and capacity per module. From the 150 WattC of the 2010s, we are now moving to modules delivering 500 WattC1. China has produced the equivalent of 288 GW of modules by 2022.
This chain is highly energy consuming and generates CO2 emissions. If we calculate these two indices, for a standard 60-cell module manufactured in China, delivering 350 WattC, we obtain respectively 120 KWH consumed and 77 kg of CO2 rejected. The same module manufactured entirely in France would have required 118 KWH and released 13 kg of CO2.
Panel recycling
We can now measure what it means to recreate a sovereign PV chain in Europe, where only basic silicon metal and PV grade silicon are available. The inclusion of recycling of losses in this value chain is essential for the sustainability of a new industrial model to avoid the waste of scarce natural resources.
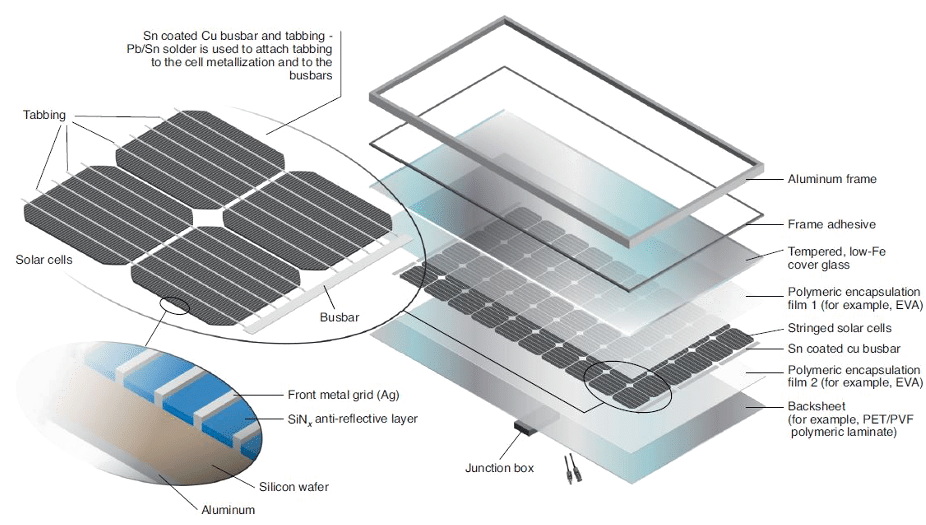
The technologies developed today now make it possible to recycle solar panels in their entirety – with the exception of polymers – including kerf’s (ROSI has developed technologies to recycle them as a replacement for fresh silicon), the aluminium frame (the circuits and technologies already exist), the glass (which has to be perfectly clean in order to be recycled by glassmakers), the copper (the circuits and technologies already exist) and the silver.
But most importantly, and this was the most difficult part, we are now able to recycle these different sources of silicon to 5N quality: recovery efficiencies are around 90% of a panel’s content. The wave of end-of-life panels combined with the recycling of kerf’s should make it possible to build a new virtuous and almost autonomous value chain in Europe.