Haptics: why give machines a sense of touch?
- Haptics refers to anything related to the sense of touch: several studies are now trying to reproduce this sense with “haptic materials”.
- Kostas Danas’ team has developed a material that can measure touch: this technology is called “haptic sensors”.
- Haptics can be very useful in the biomedical sector, such as in surgery or the fitting of prostheses.
- This technology can also help us in everyday life, for example to improve the automatic door system in lifts.
Haptics. The word may sound complex, but the concept is simple: it refers to anything related to the sense of touch. Many research teams around the world are not only trying to understand this sense, but also to reproduce it – much like a camera reproduces sight.
This field of study is not new. “Haptic sensation is a long-standing subject. Researchers have been trying to develop haptic sensors for forty years,” explains Kostas Danas, research director of the solid mechanics laboratory at École Polytechnique (IP Paris) and the CNRS.
What are haptics?
We interact with one type of haptic technology every day: haptic feedback, the feedback given to the user by a vibration that stimulates the sense of touch – like when a phone vibrates as you press a button. Similarly, it is this technology that is used in virtual reality gloves.
While stimulating the sense of touch is common in today’s technology, making haptic material – that is, reproducing this sense – remains a challenge. Since 2015, Kostas Danas and his team have been working on a material with these properties. “It is a new type of very flexible material: we make a composite from a polymer into which we put particles that are magnetisable,” continues the researcher. “In particular, we can use particles that remain permanently magnetised after the application of a magnetic field, which gives a flexible magnet. These particles come from the same type of material as those used in conventional magnets.”
When you touch something, the material distorts, and the magnetic field will change around it.
When the magnetic field is applied, the material will deform. Conversely, when it is deformed after being magnetised, it will act on the magnetic field around it. It is these properties and flexibility that give it its haptic characteristics. “When you touch something, the material will distort, and the magnetic field will change around it. This change will be measurable: we play with the alternating magnetic fields, following the deformation, to measure the touch,” explains Kostas Danas. This type of technology capable of measuring touch is called haptic sensors.
Biomedical use of haptic material
The possible uses of these haptic sensors are diverse. The flexibility of the material created makes it possible to adapt to any form of robot. “Haptic sensors have applications in all areas where there are robots. At present, there are almost no robots that have this sense of touch. Currently, they only see with cameras,” explains Kostas Danas. But adding this sense to robots can have many different uses, such as in the biomedical field, for minimally invasive surgery1.
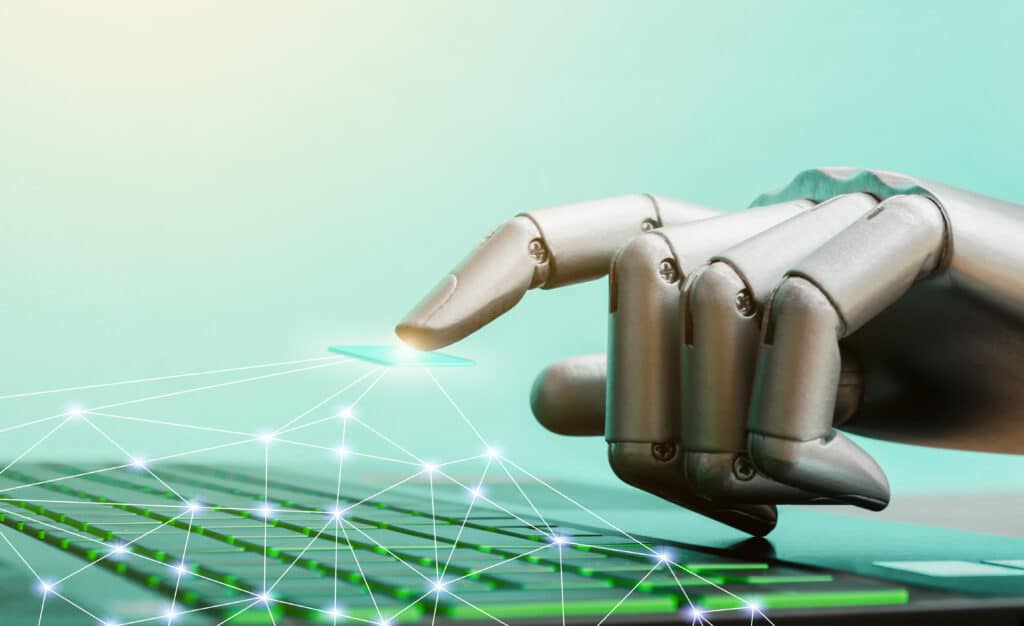
This type of surgery consists of performing an operation through a small incision and with the video-assistance, either with long instruments or on robots equipped with small cameras. But 2D video limits the possibilities of these robots: giving them an additional sense could greatly increase their capabilities and the amount of information they can return to the surgery. This would make more surgeries eligible for this type of operation, which would be beneficial to medicine, as minimally invasive surgery reduces both the risks involved and the recovery time after surgery.
Another application to be considered in the biomedical field concerns the assessment of tissue elasticity and its tactual exploration. This is usually done today by the surgeon with his or her bare hands and is extremely important for finding arteries and tumours in the body, as well as determining the quality of the patient’s tissue. However, doctors can sometimes miss nodules and small bumps during their inspection. Small robots with highly sensitive haptic capabilities could therefore assist surgeons in this process, to ensure that everything is detected.
In particular, the flexibility of the material created makes it possible to adapt to any form of robot.
Finally, it is the prostheses that could be equipped with haptic sensors. A person with a hand amputation could thus have haptic sensors in the fingers of the prosthesis, which would send sensations throughout the hand. In addition, haptic sensors should also be considered to check the fit of the prosthesis when the person performs movements. Indeed, in the long term, with the different movements of daily life, a bad fit of the prosthesis can lead to many problems in the concerned body part.
Haptics and daily habits
Haptic sensors can also be useful in everyday life and enhance existing systems. “Lifts, for example, usually have a motion sensor that prevents the doors from closing. But these sensors are photosensitive, so they stop working if the light is broken,” explains Kostas Danas, “or if they are badly placed, especially in relation to the size of children. One could then imagine haptic sensors that block the door if they sense an obstacle.”
The haptic material therefore has many possible applications as a haptic sensor, but these applications are not limited to it. “There is already a company that uses these materials to create micro-robots that deliver medicines locally to the body. As these materials are accessible with a magnet, they can be guided from the outside. They could be moved through fluids, which are otherwise complicated to pass through.”
However, the main applications of this new material are probably yet to be discovered, as Kostas Danas predicts, “applications are emerging as different people in industry or start-ups become interested.” The researcher was awarded a grant from the European Research Council this year to develop an application path for the haptic material.