Could you explain what 3D printing is and who uses it?
Fabien Szmytka. The sectors that use 3D printing (i.e., additive manufacturing) most are mainly the manufacturing and transportation industries, aerospace and motorised sports. These use 3D printers to make machines, robot parts, spare parts, machinery, casts, models, etc. The most frequently used materials are still plastic polymers in different formats (powder, thread, etc.). Only a small part of the materials used are metallic, ceramic or other types.
In the automotive industry, additive manufacturing was first used a way to make prototypes, but today it is also used to make mechanical parts as well as elements of design (car body, spoiler, etc.). For instance, car manufacturers like Honda have already built vehicles completely printed in 3D, although they are not yet marketed.
The academic world is also increasingly turning to additive manufacturing to support research. Many projects use experimental prototypes made with 3D printing technology. To this end, some laboratories or research institutions have equipped themselves with their own printers, or even Fab Labs (fabrication laboratory) like those, for example, of the Institut Pasteur (FLIP) or the Institut Polytechnique de Paris.
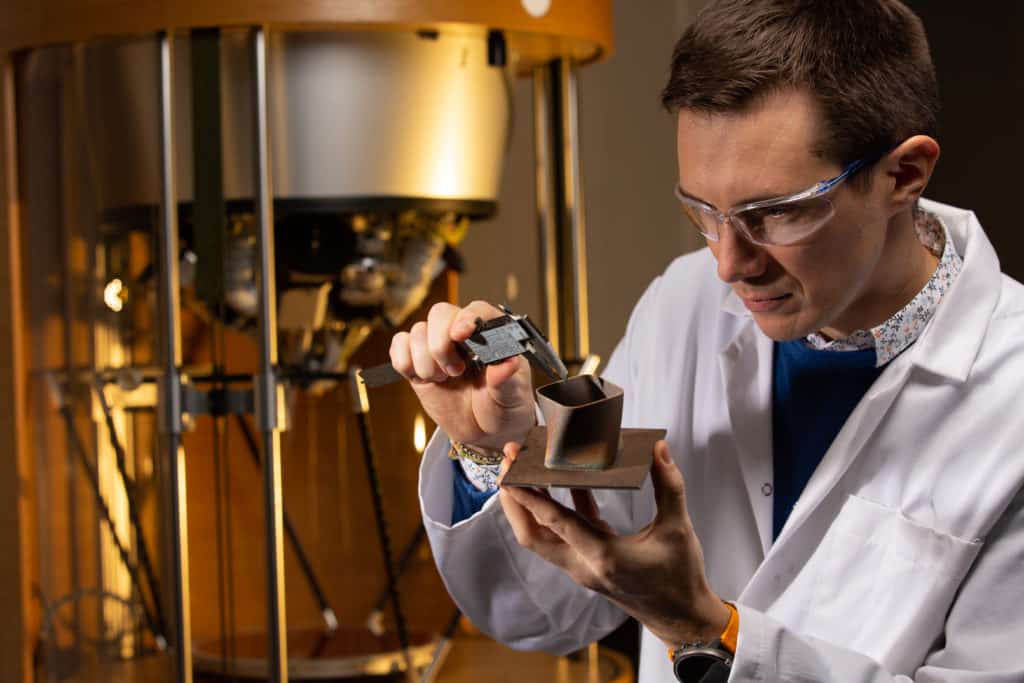
What are the main advantages of additive manufacturing in your field?
Nowadays, metallic additive fabrication makes it possible to create components with complex geometry. These would be impossible to make by using conventional methods. For example, very small details would break during demoulding in a classic foundry. In some cases, welding can be used to repair parts, but this technique is very sensitive to ambient conditions (air temperature, humidity) and very difficult to automate. You need many specialised operators, who require much long training. Additive manufacturing thus makes it possible, to some extent, to make up for the lack of specialised workers.
What does your research on metallic 3D printing consist of?
Our objective is to study metallic materials produced by additive manufacturing. We use a spraying technique based on metallic powder called “Directed Energy Deposition” to make our own materials. Their quality depends on several parameters: powder composition, power and speed of the machine. We then observe the effects of the varying these parameters on the microstructures of the material. Finally, we test the resistance of this new metallic material to mechanical stress. For instance, we evaluate the strain produced by traction, or measure the effects of heat treatment.
In our laboratory, we conduct tests on complex structures closer to the geometry of industrial parts, while standard tests use a simpler geometry (plates, cylinders). Our research on metallic materials tries to meet the demands and needs of industrial partners. For example, they can ask us to develop a material in compliance with determined characteristics for a specific use. We also lead research studies on polymers in collaboration with chemists from the CNRS.
In what fields are your studies applied? And who are the final users of these materials?
One of the most promising areas of investigation is the use of these processes to repair damaged structures. To develop applications for these metallic materials, we work with the energy, transportation and aeronautic sectors. For example, our partners EDF and SNCF use parts with very large dimensions. Their design sometimes dates back to nearly twenty years ago and, as such, they are very difficult to replace since they are not produced anymore. Hence the need to find practical and cost-effective solutions to repair them.