In recent years, 3D printing has become an important technology for medicine, especially in the field of prosthetics for dental or bone implants, but also for the substitution of amputated limbs or skin reconstruction for burn victims. More recently, other medical fields, such as cardiology, urology or neurosurgery have also started to take an interest in additive manufacturing. Moreover, ongoing research seeks to improve bioprinting of organs or tissues as a way to overcome the lack of organ donors. And the pharmaceutical sector is trying to develop medication with novel shapes or properties.
Customised printing of medical equipment
The great advantage of 3D printing is its customisation capacities: dental implants, hip, rib, sternum or knee prostheses. Hearing aids or orthopaedic insoles can also be printed as one-off objects, tailored to the needs of each patient. Bernardo Innocenti, professor in biomechanics at École polytechnique of the Université Libre de Bruxelles and president of the Belgian company CAOS (Computer Assisted Orthopaedic Surgery) works in collaboration with orthopaedic surgeons and, more specifically, with specialists in knee surgery.
He explains that the use of additive manufacturing in surgery is an interdisciplinary field, which entails ongoing dialogue between surgeons, researchers and engineers. In his opinion, the interaction between these professionals is the key to success for a biomedical product and a patient’s recovery after surgery. “3D printing is not only used to make implants, it also provides the surgeon with a maximum of important information on the organ before the surgical procedure,”he explains.
Preparing surgical procedures
Indeed, in the preoperative phase printing a three-dimensional replica of the body part can help collect vital information sometimes impossible to obtain without this technology. The surgeon can thus hold in his hand the bone or the joint, and gain precise knowledge on the shape, size, tactile characteristics, and the extent of the damage.
“Today, by using different colours and printing materials, we can truly simulate the bone and define areas of high or low bone density to decide where to put the screws and plates,” states Bernardo Innocenti. 3D printing can also be used to make personalised surgical instruments, guaranteeing a custom procedure for each patient based on the distinct position of their muscles and tendons. Surgical templates, for example, help the surgeon to define the cutting template and incision points.
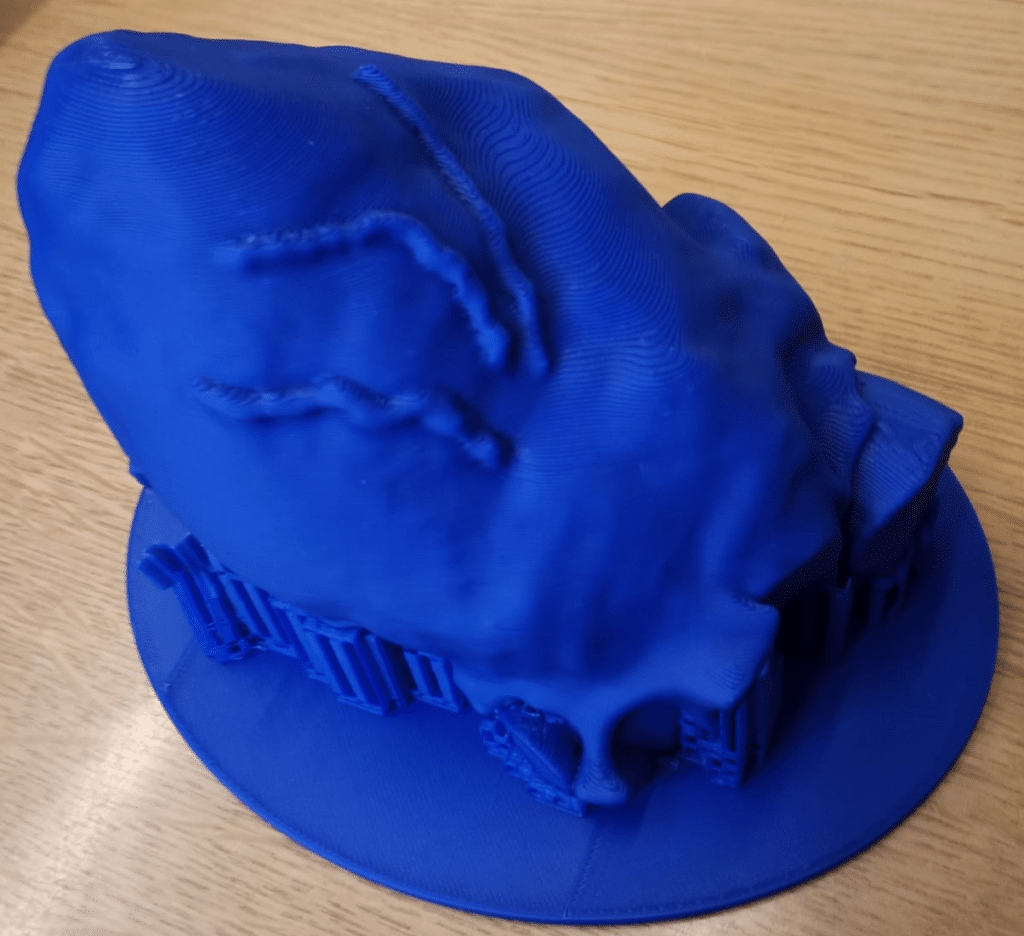
In the post-operative phase
Additive manufacturing could also prove useful in the post-operative phase, to monitor the growth of bone and prostheses/bone integration. Although, they are competing with pre-existing methods that are arguably less expensive and already very efficient.
Bernardo Innocenti insists that the use of additive manufacturing in surgery has huge advantages if all the steps are performed with extreme precision, but also if you have the necessary means and time. Indeed, the interactions between doctors and engineers, as well as the design and the modelling of the prostheses or implants, all require additional delays, while the manufacturing and installation times during the surgery are similar to other techniques.
“Though it might take a few years for 3D printing to become widely accepted by practitioners, we are already seeing an important dissemination of knowledge in medical schools”, states Bernardo Innocenti. “In the case of rare diseases, 3D printing could even help to build a database to train young surgeons.”
Recently, he even started to work in the field of cardiology, another sector in which the use of additive manufacturing is on the rise. “As in the case of the orthopaedic sector, 3D printing is not only used to manufacture protheses (valves and stents) but also because it is very precise during the surgery. Additive manufacturing does not just upgrade equipment and medication, it also improves therapy as a whole,” concludes Bernardo Innocenti.