Selon Paolo Minetola, professeur associé de technologies manufacturières de l’École polytechnique de Turin, « la fabrication additive est une technologie verte, car la production à la demande de chaque pièce utilise le minimum de matière possible et ne nécessite pas de moules ou d’outils spécifiques ».
« Elle permet une meilleure durabilité des objets à condition que l’on les conçoive correctement. On peut obtenir des formes complexes, qui sont impossibles à produire avec les technologies traditionnelles, et dont les propriétés sont améliorées (allégement, meilleur échange thermique et optimisation des flux, par exemple). »
Des gains économiques
En effet l’impression 3D polymère ne produit presque pas de chutes ou déchets et, par conséquent, permet l’économie de l’énergie nécessaire à leur stockage et leur traitement. Par ailleurs, l’utilisation de pièces avec un design plus léger (creuses mais également résistantes) réduit l’empreinte carbone de leur utilisation. Par exemple, dans tous les secteurs qu’elle touche, la production de ces nouvelles structures réduit les temps et les coûts de fabrication, mais aussi la consommation d’énergie et les émissions de gaz à effet de serre.
De plus, la fabrication des pièces peut se faire à la demande, en évitant ainsi la surproduction et le gaspillage de ressources. Et si l’on considère la grande opportunité que représente le partage des fichiers de modélisation numérique des pièces à produire avec des usines délocalisées, on comprend bien que toute la phase d’emballage et de déplacement du matériel, avec la pollution que cela engendre, peut facilement être évitée. On peut imaginer, par exemple, que dans un futur proche chaque producteur d’avion aura des imprimantes 3D pour produire rapidement les pièces de rechange des aéronefs.
Cependant, l’impact d’une nouvelle technologie – qui se décline en plusieurs techniques et utilise des matériaux très différents – n’est pas facile à évaluer, et dans la réalité du terrain, les choses sont un peu plus compliquées. La comparaison avec la fabrication traditionnelle, notamment en ce qui concerne la consommation d’énergie du cycle entier de production, n’est pas toujours possible et les études sur le sujet sont encore rares.
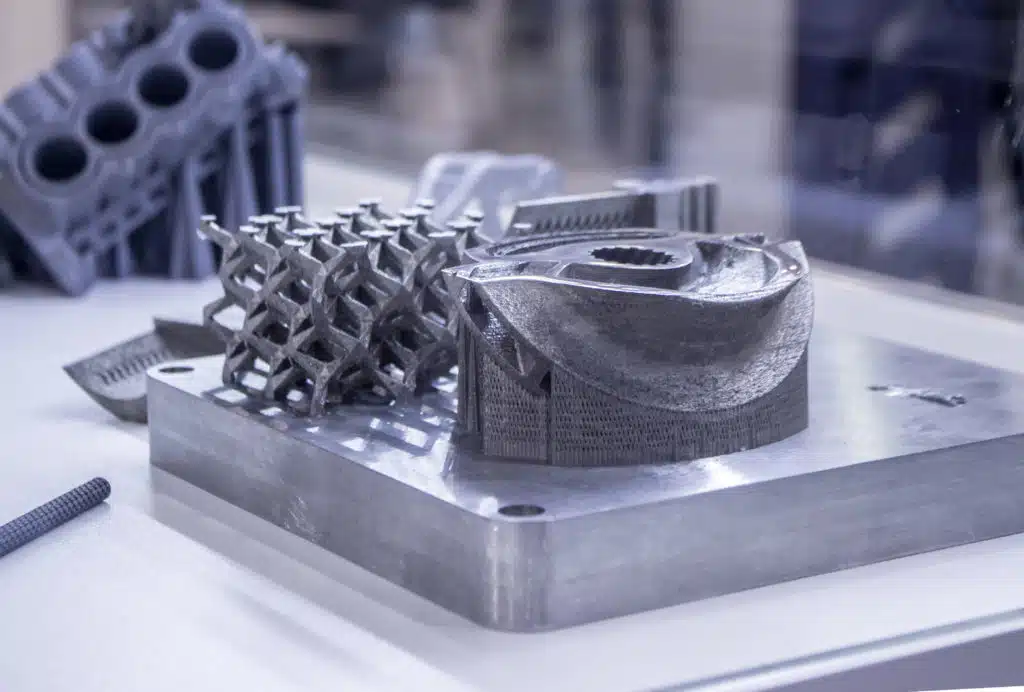
Une technologie toxique ?
Par contre, d’autres études commencent à alerter sur les risques sanitaires liés à l’impression 3D. Les gaz et les particules émises par les matériaux d’impression soumis à de hautes températures peuvent être toxiques pour la peau et les yeux, et affecter le système respiratoire. Si ces risques sont connus dans le milieu industriel et scientifique – où l’on protège les opérateurs avec des masques, des combinaisons, des respirateurs et des contrôles médicaux réguliers – ils sont moins pris en compte dans les milieux non professionnels, et notamment domestique. En outre, il n’existe pas encore de normes ISO spécifiques et universellement reconnues.
Fabien Szmytka, enseignant-chercheur à l’ENSTA Paris (IP Paris) qui travaille avec des matériaux plastiques et métalliques, regrette que l’on ne puisse pas utiliser ces procédés dans des environnements simples. « Les poudres métalliques que nous utilisons sont très fines et des protocoles stricts sont mis en place pour éviter tout risque de contamination de l’environnement et des utilisateurs. Le rendement des machines est par ailleurs faible et nous perdons beaucoup de matière. »
« Côté polymère, nous cherchons avec des chimistes du CNRS à développer des polymères recyclés ou bio-sourcés, en les alliant, par exemple, à des fibres de lin, explique Fabien Szmytka, car la composition des polymères et des résines liquides du commerce n’est pas connue pour des raisons de secret industriel. »
Une fin de vie en demi-teinte
Un autre problème se pose à la fin de vie des objets imprimés en 3D. Des systèmes sont-ils prévus pour récolter, stocker et recycler ces matériaux parfois nouveaux et dont la composition est inconnue ?
« Dans le monde médical, le recyclage de prothèses et d’implants est compliqué, principalement pour des raisons d’hygiène et de fonctionnement. Leur réutilisation n’est pas toujours possible parce qu’il s’agit souvent d’objets personnalisés qui ne seraient pas adaptés à d’autres patients et qui, de toute façon, s’abîmeraient avec les techniques classiques de stérilisation à hautes températures » explique Bernardo Innocenti, professeur en biomécanique à l’École polytechnique de l’Université Libre de Bruxelles.
« Pour toutes ces raisons, l’utilisation de matériel recyclé pour la fabrication d’implants n’est pas non plus possible pour l’instant. Le patient a le droit de recevoir le meilleur matériel possible. »
En conclusion, le chemin vers une fabrication additive complètement verte est encore long, mais ses énormes avantages par rapport à la fabrication soustractive sont déjà sous nos yeux. De nombreux concepteurs travaillent activement pour prévoir en amont tout le cycle de vie des nouveaux produits, dans une dynamique d’économie circulaire. La fabrication additive accompagnera les technologies traditionnelles en apportant ses qualités, à condition que les producteurs mettent en place de nouveaux modèles économiques, notamment grâce au soutien des politiques nationales.