Depuis ses débuts, l’aviation poursuit une quête sans fin : celle de la légèreté. Depuis les premiers engins de Clément Ader ou des frères Wright jusqu’aux avions les plus performants, la diminution du poids est un critère déterminant lors de la conception. « L’aéronautique est le secteur où le kilogramme gagné se paie le plus cher, environ cent fois plus que dans l’automobile, » souligne Patricia Krawczak, professeure à École nationale supérieure Mines-Télécom Lille Douai. En moyenne, l’industrie est prête à payer 1 euro par kilogramme gagné dans l’automobile, mais 100 € à 500 € par kilo gagné dans l’aviation civile et jusqu’à 10 000 € par kilo dans le spatial.
Aujourd’hui, la famille des matériaux les plus en vue dans cette quête est celle des composites. Composés de fibres – généralement du carbone – et d’une résine polymère formant un liant, les composites ont largement investi l’aéronautique, au point que les modèles d’avions les plus récents comme l’Airbus A380 ou le Boeing 787 en sont composés environ de moitié (contre 20 % d’aluminium, 15% de titane et 10% d’acier). « On atteint un palier, remarque Patricia Krawczak, d’autant plus que les métaux tels que le titane et l’aluminium s’améliorent aussi. » Les composites doivent donc évoluer.
Les promesses des thermoplastiques
Les ingénieurs travaillent sur plusieurs pistes. Tout d’abord, diminuer les coûts de production. En effet, si les composites présentent l’avantage d’être légers tout en garantissant de bonnes performances mécaniques, leur coût de production est encore supérieur à leur équivalent métallique. Pour produire plus vite et moins cher, les ingénieurs s’intéressent aujourd’hui aux polymères dits « thermoplastiques ». Contrairement aux polymères « thermodurcissables » qui, une fois durcis, ne peuvent plus être ramollis et travaillés, les thermoplastiques restent soudables, façonnables et même recyclables. De plus, ils n’émettent pas de composés organiques volatiles, des polluants gazeux souvent toxiques.
Cependant, la fabrication des composites à base de thermoplastiques est plus compliquée, car ces polymères sont moins fluides, et imprègnent moins facilement les fibres. C’est donc l’ensemble de la chaîne de fabrication qu’il faut revoir pour que ces matériaux puissent répondre au cahier des charges de l’industrie aéronautique. Mais en cas de succès, cela permettrait de diminuer le nombre d’assemblages, de réduire voire de revaloriser les rebuts de production et de mieux recycler les pièces en fin de vie.
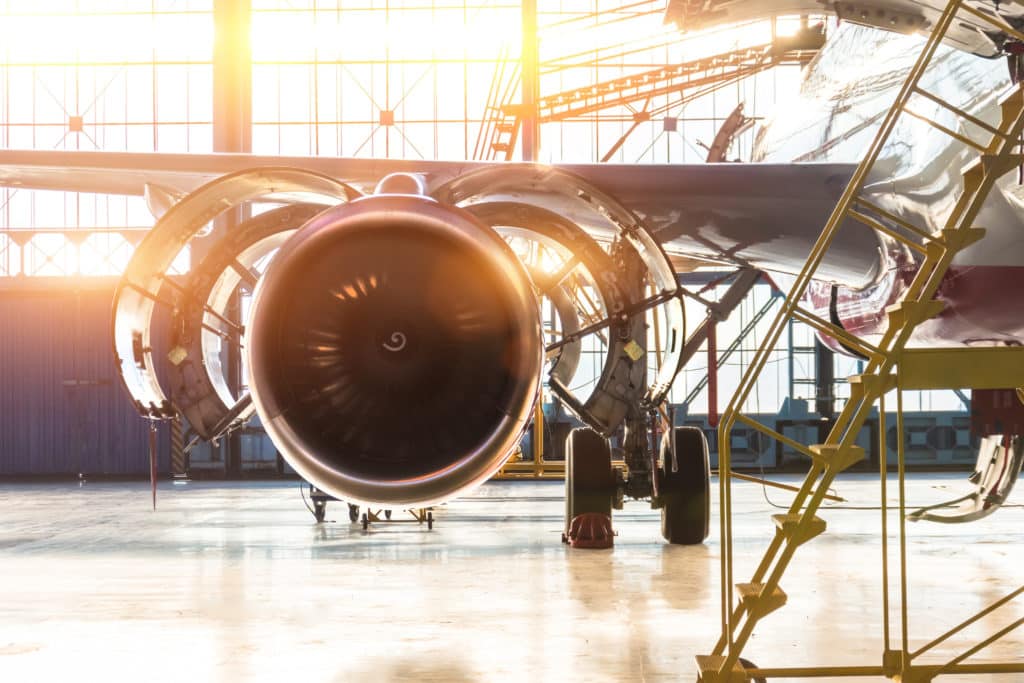
Fabrication plus souple et plus simple
Aujourd’hui, les pièces composites sont généralement fabriquées en autoclaves, sortes de grosses cocottes minutes où le composite « cuit » sous pression. Le coût de ces éléments s’élève à plusieurs centaines de milliers d’euros pour les appareils les plus performants, capables de produire des grosses pièces, à des températures et pressions élevées. Le cycle de fabrication est long, plusieurs heures pendant lesquelles l’équipement est immobilisé. « Nous travaillons sur des procédés hors autoclaves, moins coûteux et plus souples, par exemple par infusion ou injection de résine liquide directement sur une préforme fibreuse, c’est-à-dire un « squelette » de renforts fibreux, » indique la chercheuse. Cependant, la simplification de la fabrication ne doit pas se faire au détriment de la qualité, les pièces doivent allier la sécurité, la fiabilité, la performance mécanique, et ce souvent à des températures relativement hautes.
Les composites ont d’autres qualités. L’une d’elles est la multifonctionnalisation : apporter d’autres fonctions que les propriétés mécaniques. On peut par exemple rendre les composites auto-réparants, en intégrant des capsules qui libèrent des composants qui polymérisent, et ainsi « cicatrisent » la pièce endommagée. Il est également possible d’insérer des capteurs et actionneurs dans les composites pour surveiller le vieillissement et l’état de santé de la pièce ou la déformer sur commande. Autres fonctions possibles : la transmission de données ou encore la production d’énergie par piézoélectricité pour alimenter des objets connectés.
Des pièces en impression 3D
Enfin, grâce à la fabrication additive (l’impression 3D), il est désormais possible d’optimiser la forme et la structure des pièces et des composants, et de concevoir de nouvelles pièces. Les gains envisagés sont énormes : plus besoin de moule ni de découpe donc moins de gâchis de matière première. « Aujourd’hui, on sait déposer par fabrication additive du polymère renforcé de fibres coupées ou continues, expose Patricia Krawczak. Ce n’est pas encore démocratisé, notamment pour les pièces de grande taille, mais des entreprises comme Safran ou Stelia Aerospace y travaillent. » Certains avions possèdent déjà des pièces métalliques issues de fabrication additive qui ont passé tous les tests de qualification.
Si l’utilisation de nouvelles techniques de fabrication et de thermoplastique vise surtout à maintenir la part de marché des composites dans les avions, la révolution dans la conception peut, quant à elle, faire gagner 20 à 30 % de poids sur les pièces. Un allègement non négligeable dans l’objectif de réduire les émissions de gaz à effet de serre.