Cet article fait partie du deuxième numéro de notre magazine Le 3,14 dédié
à l’hydrogène. Découvrez-le ici
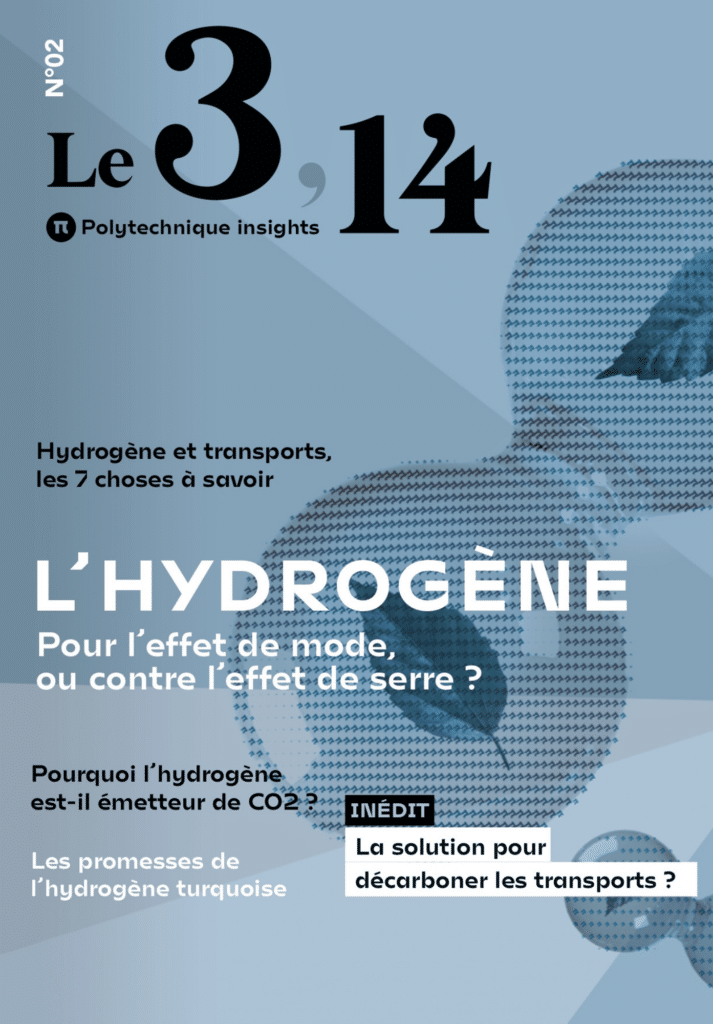
L’hydrogène gris
Par « hydrogène gris », on entend l’hydrogène produit à partir de combustibles fossiles. C’est le mode de production qui est, de très loin, le plus employé pour produire l’hydrogène aujourd’hui. C’est aussi celui qui présente le bilan carbone le plus défavorable.
Loin de son potentiel futur comme vecteur d’énergie, l’hydrogène sert actuellement surtout de matière première dans l’industrie, que ce soit dans le raffinage pétrolier pour l’hydrocraquage et la désulfuration des carburants (environ 44 % de la demande), dans la synthèse d’ammoniac pour les engrais azotés (38 %), pour la production de certains produits chimiques (8 %), ou encore dans l’industrie alimentaire et diverses autres applications (10 %). Ces besoins, qui représentent 75 millions de tonnes d’hydrogène par an à l’échelle mondiale, sont donc couverts à 48 % par le procédé de reformage du gaz naturel, à 30 % à partir d’hydrocarbures pétroliers et à 18 % par gazéification du charbon. Cette production s’accompagne de l’émission d’un milliard de tonnes de CO2 chaque année. L’électrolyse de l’eau, beaucoup moins carbonée – mais tout dépend du mix électrique utilisé – couvre à ce jour moins de 5 % de la demande.
Pourquoi les combustibles fossiles ?
Dans tous les cas, la fabrication d’hydrogène passe par la décomposition de la molécule d’eau, une opération qui demande une grande quantité d’énergie : 121 mégajoules pour produire 1 kg d’hydrogène. Dans les procédés conventionnels, une partie de cette énergie est apportée par la réaction d’un combustible avec de la vapeur d’eau à haute température. Le mélange de combustible et d’eau est alors converti par la réaction de reformage, en un mélange de monoxyde de carbone (CO) et d’hydrogène. Cette opération demande néanmoins l’apport d’un complément d’énergie, qui est apporté par la combustion de fuel ou de gaz afin de maintenir le réacteur de reformage à la bonne température opérationnelle. Après cette première étape, il est nécessaire de recourir à une opération de « water gas shift » (réaction du gaz à l’eau) afin de convertir le CO, très toxique, en CO2 par réaction avec de la vapeur d’eau à moyenne température.
Au bilan, on constate que du CO2 est généré en grande quantité aux différentes étapes du procédé : conversion du CO issu du reformeur, combustion de fuel pour la production de vapeur et pour l’apport énergétique dans le reformeur. Pour chaque tonne d’hydrogène produite, ce sont ainsi près de 12 tonnes de CO2 qui sont libérées dans l’atmosphère.
Si le reformage des combustibles fossiles reste, malgré son bilan carbone exécrable, le procédé le plus utilisé, c’est en raison d’un avantage décisif en matière de coûts. L’hydrogène issu du reformage de gaz naturel en grand volume coûte environ 1,5 €/kg, là où celui produit par électrolyse de l’eau revient à 6 €/kg. Notons néanmoins que, même au coût le plus bas, l’hydrogène revient encore 3 fois plus cher que le gaz naturel à quantité d’énergie équivalente.
En plus des problèmes de prix de revient et d’émissions de GES, l’hydrogène souffre de capacités de productions encore très insuffisantes pour représenter à ce jour une solution viable pour la transition énergétique. En effet, si elle était consacrée intégralement à la conversion d’énergie, la production mondiale actuelle d’hydrogène couvrirait à peu près 214 Mtep (millions de tonnes équivalent pétrole). Or, la demande mondiale annuelle d’énergie est de 14,5 Gtep (milliards de tep). Ainsi, il faudrait accroître la production d’un facteur 14 pour que l’hydrogène puisse couvrir 20 % de la consommation énergétique mondiale. Pour que cela ait un sens, il est évident que cela ne pourra pas se faire avec de l’hydrogène gris !
Conversion énergétique de l’hydrogène
On parlera donc ici de conversion énergétique d’hydrogène d’origine renouvelable de préférence. L’hydrogène est un composé très versatile, qui peut être converti en énergie de différentes manières :
- Sous forme thermochimique, par réaction avec des réactifs appropriés. On obtient alors une énergie potentielle, aisément stockable sur de longues durées et utilisable à la demande. Par le procédé Sabatier, en utilisant du CO2 comme réactif, on obtient du méthane synthétique qui peut ensuite servir de combustible pour l’industrie et les transports ou être injecté dans les réseaux. Ce concept est connu sous le vocable « power to gas », dans le cas où l’hydrogène utilisé provient de l’électrolyse de l’eau. Par le procédé Fischer-Tropsch, on obtient des combustibles liquides (« power to liquids »). Par le procédé Haber-Bosch on obtient, en combinant l’hydrogène avec l’azote de l’air, de l’ammoniac facilement stockable et qui peut lui-même servir de combustible.
- Sous forme de chaleur et de travail mécanique, par combustion dans l’air ou avec l’oxygène pur. C’est notamment le principe du moteur-fusée, utilisé sur certains étages des fusées Ariane. Cette solution fait partie des moyens envisagés pour propulser les futurs avions à hydrogène. L’hydrogène peut également être additionné en quantité limitée aux combustibles conventionnels, dans les réseaux de gaz naturel ou pour alimenter les moteurs à combustion interne.
- Sous forme de chaleur et de travail électrique, par oxydation ménagée dans une pile à combustible (PàC). Il existe aujourd’hui une grande variété de technologies de PàC, certaines très matures, d’autres tout juste parvenues au stade commercial, d’autres enfin, encore en développement. L’un des enjeux majeurs est d’optimiser le rendement électrique des PàC, qui se limite aux alentours de 60–65 % dans le meilleur des cas. Cela signifie que seule 60 à 65 % de l’énergie thermochimique transportée par le combustible est effectivement convertie en travail électrique, le reste étant perdu sous forme de chaleur. Si cette chaleur est produite à basse ou moyenne température (< 500 °C par exemple), elle est difficilement valorisable, alors que la chaleur produite à haute température (entre 700 et 1000 °C) peut être convertie en travail mécanique avec une bonne efficacité. C’est tout l’enjeu des piles à combustible à carbonates fondus (MCFC) ou à oxydes solides (SOFC). Quoique prometteuses pour certaines applications – fixes en général – ces technologies haute température en sont encore à un stade précoce de leur développement. Les PàC les plus employées sont celles à électrolyte liquide (solution alcaline ou acide) et à membranes échangeuses de protons (PEMFC pour « proton exchange membrane fuel cell »), qui travaillent à des températures modérées. Les PàC pour la mobilité appartiennent pour l’essentiel cette dernière technologie, qui reste néanmoins coûteuse en raison des matériaux qu’elle utilise (membrane, catalyseur à base de platine).
On peut espérer que les recherches en cours et le développement d’un marché de masse permettront aux PàC de connaître des progrès comparables à ceux réalisés par les batteries, en termes de coûts et d’efficacité, et à l’hydrogène de trouver sa place dans la transition énergétique.